Покрытие сплавами медных шин, оловянирование (лужение)
НТЦ ЭНЕРГО-РЕСУРС производит гальваническим способом шины медные луженые твердые ШМТЛ и мягкие ШММЛ.
Медные луженые шины применяются преимущественно при изготовлении оборудования повышенной надежности, эксплуатация которого предусмотрена в тяжелых климатических условиях, в агрессивных промышленных средах, в условиях повышенной влажности и воздействия морского воздуха. Медные луженые шины можно соединять с алюминиевыми проводниками без дополнительных элементов соединения.
Рассмотрим технологии оловянирования (лужения) медных шин и преимущества луженых шин перед обычными медными шинами.
Основные способы лужения (оловянирования)
Существуют три метода нанесения защитного покрытия:
- горячий способ;
- контактное осаждение;
- гальваническое осаждение
Горячее лужение считается классическим способом, поскольку именно с него начиналось развитие технологии. В зависимости от условий выполнения работ защитный слой может быть нанесен двумя методами:
- Погружение. Заготовку опускают в резервуар с оловом, нагретым до рабочей температуры.
- Растирание. Сплав наносят непосредственно на подготовленную деталь, разогретую, после чего равномерно распределяют по всей поверхности. Деталь можно разогревать различными способами, например паяльной лампой, паяльником отдельный участок и.т.п.
Горячий способ лужения отличается своей простотой. Для выполнения работ не нужно приобретать специального инструмента или обладать профессиональными знаниями. Основной недостаток – неравномерное покрытие заготовки. Это справедливо как для погружения, так и для растирания. Особенно ярко он проявляется при обработке деталей со сложной криволинейной поверхностью. Кроме того, данный способ особенно требователен к чистоте рабочего сплава. Чужеродные элементы, попадающие в рабочую смесь, удалить практически невозможно.
Химическое лужение или контактное осаждение применяется при производстве печатных плат. Процесс является контактным и основан на осаждении олова из раствора его комплексной соли за счет разности потенциалов, возникающей между медью и оловом. Толщина получаемого покрытия около 1 мкм. При этом не требуется контролировать время нанесения покрытия. Скорость осаждения олова снижается по мере перекрытия медной основы, пока процесс не прекратиться полностью. Толщина осадка определяется составом раствора и режимом процесса и должна быть практически одинаковой на всех участках, контактирующих с раствором. Недостатком контактного метода нанесения оловянного покрытия является малая толщина покрытия. Нанесение оловянного покрытия на медные проводники печатных схем дает возможность производить пайку некоррозионными флюсами, а также повысить качество плат за счет устранения перегрева при пайке
Гальваническое лужение – современный способ нанесения покрытия, когда в ходе протекания электрохимической реакции, ионы меди на поверхности замещаются ионами олова из оловосодержащего раствора. Только электрохимический способ позволяет получить покрытие заданной толщины практически на любом металле. Раствор при гальванической обработке может иметь щелочную или кислотную основу. Щелочные электролиты используют для оловянирования меди, других цветных металлов и их сплавов, имеющих сложную конфигурацию. Они имеют высокую рассеивающую способность, покрытие характеризуется мелкокристаллической структурой. Осаждение олова происходит медленно и необходимо, чтобы электролит имел температуру не меньше 70°С.
Независимо от типа электролита катализатором процесса является электрический ток, который активизирует рабочий процесс. К положительным сторонам электрохимического метода оловянирования относят:
- равномерное распределение сплава по всей плоскости;
- толщина слоя регулируется с помощью изменения параметров тока;
- отсутствуют ограничения по сложности поверхности обрабатываемых изделий;
- экономный расход смеси;
- защитный слой обладает лучшими параметрами.
Единственный недостаток гальванического лужения – высокая себестоимость, поскольку рабочий процесс сопровождается большим расходом энергии, а для контроля необходимо постоянное присутствие специалиста высокой квалификации. Лужение с использованием электролита связано со сложностью приготовления раствора. В ходе процесса должен вестись постоянный контроль концентрации щелочи или кислоты в электролите, а также состояния анодов и поверхности ванны.
Коррозионная стойкость шины медной луженой
Оловянное покрытие на медной токоведущей (заземляющей) шине является анодным (или протекторным) т.е. электрохимический потенциал олова отрицательнее, чем меди. Это означает, что в коррозионно-активной среде в первую очередь будет разрушаться олово и только после полного растворения олова на определенном участке будет повреждаться медь. Само по себе олово является достаточно стойким к коррозии металлом, поэтому применение оловянного покрытия на медной шине значительно увеличивает срок службы такой шины. Для увеличения коррозионной стойкости оловянного покрытия на медной шине покрытие осаждается из электролита с блескообразователями и может легироваться висмутом (т.е. осаждается сплав олово-висмут). Оловянное покрытие (особенно блестящее) безпористое начиная с толщины 6 мкм.
Электропроводность луженой медной шины
Несмотря на то, что олово хуже проводит электричество, чем чистая медь, оно уверенно занимает второе место после меди, если не считать покрытия драгоценными металлами, что очень дорого.
Уплотнение контактов на луженой медной шине
Интересным свойством покрытия оловом в контактных отверстиях на токоведущих (заземляющих) шинах является свойство уплотнителя. Олово – мягкий пластичный металл, который легко может уплотнять как резьбовые, так и нерезьбовые контакты. Уплотненные контакты, соответственно, более надежны, а сопротивление в них – ниже.
Сплавы, применяемые для оловянирования/лужения медных шин
Сплавы Sn-Pb (олово-свинец) с содержанием олова 10…60% применяются в электронной, радиотехнической и приборостроительной промышленности. Они хорошо паяются и сохраняют способность к пайке, в отличие от оловянных покрытий, в течение длительного времени. Способность к пайке и длительность сохранения этого свойства повышается при оплавлении. Сплавы Sn-Pb – мягкие, пластичные. Они менее склонны к образованию игл. При образовании гальванических пар они катодны по отношению к железу и анодны по отношению к меди.
Покрытия сплавом Sn-Pb наносят на медную шину непосредственно. Они могут быть использованы для всех условий эксплуатации, включая ОЖ – очень жесткие. (Защитные покрытия по условиям эксплуатации делят на группы легкие — Л средние — С жесткие — Ж очень жесткие — ОЖ. Эти покрытия классифицируют по способу получения, материалу, физико-химическим и декоративным свойствам. Технология нанесения покрытий и методы контроля их качества приведены в ГОСТ 16976—71. ) Сплавы Sn — Pb с содержанием 5…11% олова применяются как антифрикционные в условиях сухого и полусухого трения. Толщина слоя для условий Л (легкие) – 6…9 мкм, для условий С и Ж (средние и жесткие)- 18…20 мкм.
Сплавы Sn-Bi (олово-висмут) с содержанием висмута 0,5…2,0% применяются в электронной, радиотехнической и приборостроительной промышленности. Сплав хорошо паяется и длительное время сохраняет способность к пайке. Сплав Sn-Bi менее склонен к образованию игл чем олово.
Достоинства оловянного покрытия (олово-висмут) медных шин:
- Оловянное покрытие в атмосферных условиях является анодным по отношению к меди и ее сплавам, поэтому защита сплавом олово-висмут позволяет значительно увеличить коррозионную стойкость покрытых изделий. Увеличение коррозионной стойкости дает также осаждение блестящего оловянного покрытия вместо матового, что объясняется меньшей пористостью блестящих покрытий;
- Покрытие олово-висмут значительно повышает паяемость поверхностей медных деталей. Блестящее покрытие сохраняет эту способность более длительное время, чем матовое, а легирование покрытия висмутом позволяет сохранить способность к пайке дольше одного года;
- Покрытие олово-висмут устойчиво к воздействию серосодержащих соединений и может применяться на деталях, контактирующих со всеми видами пластмасс и резин;
- Оловянное покрытие обладает хорошим сцеплением с основным металлом, эластичностью, выдерживает изгиб, вытяжку, развальцовку, штамповку, прессовую посадку, хорошо сохраняется при свинчивании, герметизирует резьбовые соединения;
- Блестящее оловяное покрытие беспористо при толщине слоя больше 5 мкм (матовое покрытие оловом значительно пористо).
Пористость покрытий с толщиной до 5 мкм может быть снижена оплавлением;
- Легирование висмутом (0,5-2%) позволяет предотвратить “иглообразование”, а также позволяет избежать разрушения покрытия при эксплуатации ниже минус 30°С. Разрушение оловянных покрытий БЕЗ висмута происходит вследствие перехода компактного белого олова (β-Sn) в порошкообразное серое олово (α-Sn) («оловянная чума»).
Недостатки оловянного покрытия (олово-висмут) на меди, латуни, бронзе:
- Низкая износостойкость;
- Более низкая, по сравнению с олово-свинцом пластичность;
- Более низкие, по сравнению с олово-свинцом и свинцом антифрикционные свойства;
- Наличие в составе висмута не позволяет использовать покрытие в пищевых целях;
- Покрытие нестойко в щелочной среде.
По теме
Шины медные луженые ШМТЛ, ШММЛ, пластины переходные луженые
ХИМИЧЕСКОЕ ЛУЖЕНИЕ МЕДИ И МЕДНЫХ СПЛАВОВ
Использование данной таблицы поможет Вам подобрать нужный комплект для металлопокрытия. Вам только надо знать какой металл Вы хотите использовать в качестве металлопокрытия и основу — базовый металл или сплав, на который оно будет наноситься.
Анодирование АлюминияХромированной поверхностиМеди, латуни, бронзыНе токопроводящих материаловЖелеза и сталиЛегированной и закаленной сталиЦинка, свинца, свинцовых сплавовНикеляОловаЗолота
Золочение АлюминияХромированной поверхностиМеди, латуни, бронзыНе токопроводящих материаловЖелеза и сталиЛегированной и закаленной сталиЦинка, свинца, свинцовых сплавов НикеляОловаЗолота
Копи-хромирование АлюминияХромированной поверхности Меди, латуни, бронзыНе токопроводящих материаловЖелеза и сталиЛегированной и закаленной стали Цинка, свинца, свинцовых сплавовНикеля ОловаЗолота
Лужение АлюминияХромированной поверхностиМеди, латуни, бронзыНе токопроводящих материаловЖелеза и сталиЛегированной и закаленной сталиЦинка, свинца, свинцовых сплавовНикеляОловаЗолота
Меднение АлюминияМеди, латуни или бронзыХромированной поверхностиНе токопроводящих материаловЖелеза и сталиЛегированной и закаленной сталиЦинка, свинца, свинцовых сплавовНикеляОловаЗолота
Никелирование АлюминияМеди, латуни, бронзыХромированной поверхности Не токопроводящих материаловЖелеза и сталиЛегированной и закаленной стали Цинка, свинца, свинцовых сплавовНикеляОловаЗолота
Серебрение АлюминияХромированной поверхностиМеди, латуни, бронзыНе токопроводящих материаловЖелеза и сталиЛегированной и закаленной стали Цинка, свинца, свинцовых сплавовНикеляОловаЗолота
Цинкование АлюминияМеди, латуни, бронзыХромированной поверхностиНе токопроводящих материаловЖелеза и сталиЛегированной и закаленной сталиЦинка, свинца, свинцовых сплавовНикеляОловаЗолота
Чернение Железа и сталиМеди, латуни и бронзы
Хромирование АлюминияХромированной поверхности Меди, латуни, бронзыНе токопроводящих материаловЖелеза и стали Легированной и закаленной стали Цинка, свинца, свинцовых сплавовНикеля ОловаЗолота
Анодирование — Алюминия
Анодирование создает прочный износостойкий слой на алюминиевой поверхности.
Перед проведением процесса анодирования, алюминиевую поверхность рекомендуется обработать в травильно-осветлительном cоставе:
- Используйте для этого «Травильно-осветлительный состав»
После этого, проводится анодирование алюминиевой поверхности. Используйте для этого представленный комплект:
- Комплект «Анодирование алюминия»
Вернуться к подбору комплекта
Золочение — Алюминия
Для того, чтобы нанести металлическое покрытие на алюминий, вы должны сначала провести предварительную подготовку его поверхности. Для этого алюминиевую деталь обрабатывают сначала в растворе универсального очистителя. Используйте для этого представленный состав:
- Состав «Универсальный очиститель»
После этого деталь рекомендуется обработать в травильно-осветлительном составе. Используйте для этого представленный комплект:
После обработки в травильно-осветлительном составе, можно использовать 2 варианта обработки алюминиевой поверхности перед нанесением конечного декоративного покрытия.
1 вариант (используя реактив «Цинкатный активатор»)
Проведите цинкатную обработку и осветление алюминиевой поверхности.
Используйте для этого представленный комплект:
После цинкатной обработки, на деталь необходимо нанести покрытие “первичная медь”. Используйте для этого представленный комплект:
После этого, для повышения конечного блеска на деталь рекомендуется дополнительно нанести покрытие “блестящая медь”.
Используйте для этого представленный комплект:
После этого можно проводить золочение металлической поверхности. Используйте для этого представленный электролит:
2 вариант (используя реактив «Первичный никель»*)
*Не может использоваться для кремнийсодержащих алюминиевых сплавов.
Обработайте деталь в реактиве “первичный никель”. Используйте для этого представленный комплект:
После этого, для повышения конечного блеска покрытия, на деталь рекомендуется нанести покрытие “блестящая медь”. Используйте для этого представленный комплект:
После этого можно проводить золочение металлической поверхности. Используйте для этого представленный электролит:
Вернуться к подбору комплекта
Копи-хромирование — Алюминия
После этого деталь рекомендуется обработать в травильно-осветлительном составе. Используйте для этого представленный комплект:
После обработки в травильно-осветлительном составе, можно использовать 2 варианта обработки алюминиевой поверхности перед нанесением конечного декоративного покрытия.
1 вариант (используя реактив «Цинкатный активатор»)
Проведите цинкатную обработку и осветление алюминиевой поверхности.
Используйте для этого представленный комплект:
После цинкатной обработки, на деталь необходимо нанести покрытие “первичная медь”. Используйте для этого представленный комплект:
После этого, для повышения конечного блеска на деталь рекомендуется дополнительно нанести покрытие “блестящая медь”.
Используйте для этого представленный комплект:
После этого на металлическую поверхность наносится покрытие «КОПИ-ХРОМ». Используйте для этого представленный комплект:
2 вариант (используя реактив «Первичный никель»*)
*Не может использоваться для кремнийсодержащих алюминиевых сплавов.
Обработайте деталь в реактиве “первичный никель”. Используйте для этого представленный комплект:
После этого, для повышения конечного блеска покрытия, на деталь рекомендуется нанести покрытие “блестящая медь”. Используйте для этого представленный комплект:
После этого на металлическую поверхность наносится покрытие «КОПИ-ХРОМ». Используйте для этого представленный комплект:
Вернуться к подбору комплекта
Лужение — Алюминия
Для того, чтобы нанести металлическое покрытие на алюминий, вы должны сначала провести предварительную подготовку его поверхности. Для этого алюминиевую деталь обрабатывают сначала в растворе универсального очистителя. Используйте для этого представленный состав:
После этого деталь рекомендуется обработать в травильно-осветлительном составе. Используйте для этого представленный комплект:
После обработки в травильно-осветлительном составе, можно использовать 2 варианта обработки алюминиевой поверхности перед нанесением конечного декоративного покрытия.
1 вариант (используя реактив «Цинкатный активатор»)
Проведите цинкатную обработку и осветление алюминиевой поверхности.
Используйте для этого представленный комплект:
После цинкатной обработки, на деталь необходимо нанести покрытие “первичная медь”.
После этого, для повышения конечного блеска на деталь рекомендуется дополнительно нанести покрытие “блестящая медь”.
Используйте для этого представленный комплект:
После этого можно проводить процесс блестящего лужения. Используйте для этого представленный комплект:
2 вариант (используя реактив «Первичный никель»*)
*Не может использоваться для кремнийсодержащих алюминиевых сплавов.
Обработайте деталь в реактиве “первичный никель”. Используйте для этого представленный комплект:
После этого, для повышения конечного блеска покрытия, на деталь рекомендуется нанести покрытие “блестящая медь”. Используйте для этого представленный комплект:
После этого можно проводить процесс блестящего лужения. Используйте для этого представленный комплект:
Вернуться к подбору комплекта
Меднение — Алюминия
Для того, чтобы нанести металлическое покрытие на алюминий, вы должны сначала провести предварительную подготовку его поверхности. Для этого алюминиевую деталь обрабатывают сначала в растворе универсального очистителя. Используйте для этого представленный состав:
После этого деталь рекомендуется обработать в травильно-осветлительном составе. Используйте для этого представленный комплект:
После обработки в травильно-осветлительном составе, можно использовать 2 варианта обработки алюминиевой поверхности перед нанесением конечного декоративного покрытия.
1 вариант (используя реактив «Цинкатный активатор»)
Проведите цинкатную обработку и осветление алюминиевой поверхности.
Используйте для этого представленный комплект:
После цинкатной обработки, на деталь необходимо нанести покрытие “первичная медь”. Используйте для этого представленный комплект:
После этого можно проводить процесс блестящего меднения. Используйте для этого представленный комплект:
2 вариант (используя реактив «Первичный никель»*)
*Не может использоваться для кремнийсодержащих алюминиевых сплавов.
Обработайте деталь в реактиве “первичный никель”. Используйте для этого представленный комплект:
После этого можно проводить процесс блестящего меднения. Используйте для этого представленный комплект:
Вернуться к подбору комплекта
Никелирование — Алюминия
Для того, чтобы нанести металлическое покрытие на алюминий, вы должны сначала провести предварительную подготовку его поверхности. Для этого алюминиевую деталь обрабатывают сначала в растворе универсального очистителя. Используйте для этого представленный состав:
После этого деталь рекомендуется обработать в травильно-осветлительном составе. Используйте для этого представленный комплект:
После обработки в травильно-осветлительном составе, можно использовать 2 варианта обработки алюминиевой поверхности перед нанесением конечного декоративного покрытия.
1 вариант (используя реактив «Цинкатный активатор»)
Проведите цинкатную обработку и осветление алюминиевой поверхности.
Используйте для этого представленный комплект:
После цинкатной обработки, на деталь необходимо нанести покрытие “первичная медь”. Используйте для этого представленный комплект:
После этого, для повышения конечного блеска на деталь рекомендуется дополнительно нанести покрытие “блестящая медь”.
Используйте для этого представленный комплект:
После этого можно проводить процесс блестящего никелирования. Используйте для этого представленный комплект:
2 вариант (используя реактив «Первичный никель»*)
*Не может использоваться для кремнийсодержащих алюминиевых сплавов.
Обработайте деталь в реактиве “первичный никель”. Используйте для этого представленный комплект:
После этого, для повышения конечного блеска покрытия, на деталь рекомендуется нанести покрытие “блестящая медь”. Используйте для этого представленный комплект:
После этого можно проводить процесс блестящего никелирования. Используйте для этого представленный комплект:
Вернуться к подбору комплекта
Серебрение — Алюминия
Для того, чтобы нанести металлическое покрытие на алюминий, вы должны сначала провести предварительную подготовку его поверхности. Для этого алюминиевую деталь обрабатывают сначала в растворе универсального очистителя. Используйте для этого представленный состав:
После этого деталь рекомендуется обработать в травильно-осветлительном составе. Используйте для этого представленный комплект:
После обработки в травильно-осветлительном составе, можно использовать 2 варианта обработки алюминиевой поверхности перед нанесением конечного декоративного покрытия.
1 вариант (используя реактив «Цинкатный активатор»)
Проведите цинкатную обработку и осветление алюминиевой поверхности.
Используйте для этого представленный комплект:
После цинкатной обработки, на деталь необходимо нанести покрытие “первичная медь”. Используйте для этого представленный комплект:
После этого, для повышения конечного блеска на деталь рекомендуется дополнительно нанести покрытие “блестящая медь”.
Используйте для этого представленный комплект:
После этого можно проводить процесс блестящего серебрения. Используйте для этого представленный электролит:
2 вариант (используя реактив «Первичный никель»*)
*Не может использоваться для кремнийсодержащих алюминиевых сплавов.
Обработайте деталь в реактиве “первичный никель”. Используйте для этого представленный комплект:
После этого, для повышения конечного блеска покрытия, на деталь рекомендуется нанести покрытие “блестящая медь”. Используйте для этого представленный комплект:
После этого можно проводить процесс блестящего серебрения. Используйте для этого представленный электролит:
Вернуться к подбору комплекта
Цинкование — Алюминия
Для того, чтобы нанести металлическое покрытие на алюминий, вы должны сначала провести предварительную подготовку его поверхности. Для этого алюминиевую деталь обрабатывают сначала в растворе универсального очистителя. Используйте для этого представленный состав:
После этого деталь рекомендуется обработать в травильно-осветлительном составе. Используйте для этого представленный комплект:
После обработки в травильно-осветлительном составе, можно использовать 2 варианта обработки алюминиевой поверхности перед нанесением конечного декоративного покрытия.
1 вариант (используя реактив «Цинкатный активатор»)
Проведите цинкатную обработку и осветление алюминиевой поверхности.
Используйте для этого представленный комплект:
После цинкатной обработки, на деталь необходимо нанести покрытие “первичная медь”. Используйте для этого представленный комплект:
После этого, для повышения конечного блеска на деталь рекомендуется дополнительно нанести покрытие “блестящая медь”.
Используйте для этого представленный комплект:
Теперь можно проводить процесс блестящего цинкования. Используйте для этого представленный комплект:
2 вариант (используя реактив «Первичный никель»*)
*Не может использоваться для кремнийсодержащих алюминиевых сплавов.
Обработайте деталь в реактиве “первичный никель”. Используйте для этого представленный комплект:
После этого, для повышения конечного блеска покрытия, на деталь рекомендуется нанести покрытие “блестящая медь”. Используйте для этого представленный комплект:
Теперь можно проводить процесс блестящего цинкования. Используйте для этого представленный комплект:
Вернуться к подбору комплекта
Хромирование — Алюминия
Для того, чтобы нанести металлическое покрытие на алюминий, вы должны сначала провести предварительную подготовку его поверхности. Для этого алюминиевую деталь обрабатывают сначала в растворе универсального очистителя. Используйте для этого представленный состав:
После этого деталь рекомендуется обработать в травильно-осветлительном составе. Используйте для этого представленный комплект:
После обработки в травильно-осветлительном составе, можно использовать 2 варианта обработки алюминиевой поверхности перед нанесением конечного декоративного покрытия.
1 вариант (используя реактив «Цинкатный активатор»)
Проведите цинкатную обработку и осветление алюминиевой поверхности.
Используйте для этого представленный комплект:
После цинкатной обработки, на деталь необходимо нанести покрытие “первичная медь”. Используйте для этого представленный комплект:
После этого, для повышения конечного блеска на деталь рекомендуется дополнительно нанести покрытие “блестящая медь”.
Используйте для этого представленный комплект:
После этого, можно проводить процесс декоративного хромирования. Используйте для этого любой из представленных комплектов:
или
2 вариант (используя реактив «Первичный никель»*)
*Не может использоваться для кремнийсодержащих алюминиевых сплавов.
Обработайте деталь в реактиве “первичный никель”. Используйте для этого представленный комплект:
После этого, для повышения конечного блеска покрытия, на деталь рекомендуется нанести покрытие “блестящая медь”. Используйте для этого представленный комплект:
После этого, можно проводить процесс декоративного хромирования. Используйте для этого любой из представленных комплектов:
или
Вернуться к подбору комплекта
Меднение — Меди, латуни или бронзы
Перед нанесением блестящего медного покрытия на медь, латунь или бронзу, необходимо сначала провести предварительную очистку и затем активацию металлической поверхности. Используйте для этого представленные составы:
- Состав «Универсальный очиститель»
- Состав «Химический активатор»
После этого можно проводить процесс блестящего меднения. Используйте для этого представленный комплект:
Вернуться к подбору комплекта
Никелирование — Меди, латуни, бронзы
Перед никелированием меди, латуни или бронзы, необходимо сначала провести очистку и активацию металлической поверхности. Используйте для этого представленные составы:
- Состав «Универсальный очиститель»
- Состав «Химический активатор»
После этого можно проводить процесс блестящего никелирования. Используйте для этого представленный комплект:
Вернуться к подбору комплекта
Цинкование — Меди, латуни, бронзы
Перед цинкованием меди, латуни или бронзы, необходимо сначала провести предварительную очистку и активацию металлической поверхности. Используйте для этого представленные составы:
- Состав «Универсальный очиститель»
- Состав «Химический активатор»
Теперь можно проводить процесс блестящего цинкования. Используйте для этого представленный комплект:
Вернуться к подбору комплекта
Золочение — Хромированной поверхности
Блестящее декоративное хромирование представляет собой трехслойное металлическое покрытие состоящее из первичного слоя меди, наносимого на основу для повышения адгезионных и отражательных свойств покрытия, слоя никеля, используемого для повышения его антикоррозийных свойств, и конечного слоя хрома, использующегося в качестве блестящего декоративного покрытия, и обладающего именно в такой связке, одновременно и зеркальным блеском, и исключительными антикоррозионными свойствами. На поверхности хрома в обычных условиях имеется инертная оксидная пленка, которая при нанесении на него другого металлопокрытия не обеспечивает ему достаточного сцепления и поэтому, перед нанесением другого металлопокрытия, необходимо удалить весь слой хрома. Используйте для этого представленный состав:
После удаления слоя хрома, можно заметить покрытие, имеющее едва заметный желтоватый оттенок, это слой никеля. Никелевое покрытие, перед проведением процесса хромирования, необходимо активировать. Используйте для этого представленный состав:
После этого, можно проводить золочение металлической поверхности. Используйте для этого представленный электролит:
Вернуться к подбору комплекта
Копи-хромирование — Хромированной поверхности
Блестящее декоративное хромирование представляет собой трехслойное металлическое покрытие состоящее из первичного слоя меди, наносимого на основу для повышения адгезионных и отражательных свойств покрытия, слоя никеля, используемого для повышения его антикоррозийных свойств, и конечного слоя хрома, использующегося в качестве блестящего декоративного покрытия, и обладающего именно в такой связке, одновременно и зеркальным блеском, и исключительными антикоррозионными свойствами. На поверхности хрома в обычных условиях имеется инертная оксидная пленка, которая при нанесении на него другого металлопокрытия не обеспечивает ему достаточного сцепления и поэтому, перед нанесением другого металлопокрытия, необходимо удалить весь слой хрома. Используйте для этого представленный состав:
После удаления слоя хрома, можно заметить покрытие, имеющее едва заметный желтоватый оттенок, это слой никеля. Перед нанесением покрытия “КОПИ-ХРОМ”, никель необходимо активировать. Используйте для этого представленный состав:
После этого можно наносить покрытие «КОПИ-ХРОМ». Используйте для этого представленный комплект:
Вернуться к подбору комплекта
Лужение — Хромированной поверхности
Блестящее декоративное хромирование представляет собой трехслойное металлическое покрытие состоящее из первичного слоя меди, наносимого на основу для повышения адгезионных и отражательных свойств покрытия, слоя никеля, используемого для повышения его антикоррозийных свойств, и конечного слоя хрома, использующегося в качестве блестящего декоративного покрытия, и обладающего именно в такой связке, одновременно и зеркальным блеском, и исключительными антикоррозионными свойствами. На поверхности хрома в обычных условиях имеется инертная оксидная пленка, которая при нанесении на него другого металлопокрытия не обеспечивает ему достаточного сцепления и поэтому, перед нанесением другого металлопокрытия, необходимо удалить весь слой хрома. Используйте для этого представленный состав:
После удаления слоя хрома, можно заметить покрытие, имеющее едва заметный желтоватый оттенок, это слой никеля. Перед проведением процесса лужения, его необходимо активировать. Используйте для этого представленный состав:
После этого можно проводить процесс блестящего лужения. Используйте для этого представленный комплект:
Вернуться к подбору комплекта
Серебрение — Хромированной поверхности
Блестящее декоративное хромирование представляет собой трехслойное металлическое покрытие состоящее из первичного слоя меди, наносимого на основу для повышения адгезионных и отражательных свойств покрытия, слоя никеля, используемого для повышения его антикоррозийных свойств, и конечного слоя хрома, использующегося в качестве блестящего декоративного покрытия, и обладающего именно в такой связке, одновременно и зеркальным блеском, и исключительными антикоррозионными свойствами. На поверхности хрома в обычных условиях имеется инертная оксидная пленка, которая при нанесении на него другого металлопокрытия не обеспечивает ему достаточного сцепления и поэтому, перед нанесением другого металлопокрытия, необходимо удалить весь слой хрома. Используйте для этого представленный состав:
После удаления слоя хрома, можно заметить покрытие, имеющее едва заметный желтоватый оттенок, это слой никеля. Перед проведением процесса серебрения, его необходимо активировать. Используйте для этого представленный состав:
После этого можно проводить процесс блестящего серебрения. Используйте для этого представленный электролит:
Вернуться к подбору комплекта
Хромирование — Хромированной поверхности
Блестящее декоративное хромирование представляет собой трехслойное металлическое покрытие состоящее из первичного слоя меди, наносимого на основу для повышения адгезионных и отражательных свойств покрытия, слоя никеля, используемого для повышения его антикоррозийных свойств, и конечного слоя хрома, использующегося в качестве блестящего декоративного покрытия, и обладающего именно в такой связке, одновременно и зеркальным блеском, и исключительными антикоррозионными свойствами. На поверхности хрома в обычных условиях имеется инертная оксидная пленка, которая при нанесении на него другого металлопокрытия не обеспечивает ему достаточного сцепления и поэтому, перед нанесением другого металлопокрытия, необходимо удалить весь слой хрома. Используйте для этого представленный состав:
После удаления слоя хрома, можно заметить покрытие, имеющее едва заметный желтоватый оттенок, это слой никеля. Никелевое покрытие, перед проведением процесса хромирования, необходимо активировать. Используйте для этого представленный состав:
После этого, можно проводить процесс декоративного хромирования. Используйте для этого любой из представленных комплектов:
или
Вернуться к подбору комплекта
Золочение — Меди, латуни, бронзы
Перед золочением меди, латуни или бронзы, необходимо сначала провести предварительную очистку и затем активацию металлической поверхности. Используйте для этого представленные составы:
- Состав «Универсальный очиститель»
- Состав «Химический активатор»
После этого, для повышения антикоррозионных свойств покрытия, перед проведением процесса золочения, рекомендуется нанести на металлическую поверхность слой никеля. Используйте для этого любой из представленных комплектов:
После этого можно проводить процесс золочения. Используйте для этого представленный электролит:
Вернуться к подбору комплекта
Копи-хромирование — Меди, латуни, бронзы
Перед нанесением покрытия «КОПИ-ХРОМ» на медь, латунь или бронзу, необходимо сначала провести предварительную очистку и затем активацию металлической поверхности. Используйте для этого представленные составы:
- Состав «Универсальный очиститель»
- Состав «Химический активатор»
После этого для повышения блеска и износостойкости конечного покрытия, на металлическую поверхность наносится блестящее медное покрытие. Используйте для этого представленный комплект:
Теперь можно наносить покрытие «КОПИ-ХРОМ». Используйте для этого представленный комплект:
Вернуться к подбору комплекта
Лужение — Меди, латуни, бронзы
Перед лужением меди, латуни или бронзы, необходимо сначала провести предварительную очистку и затем активацию металлической поверхности. Используйте для этого представленные составы:
- Состав «Универсальный очиститель»
- Состав «Химический активатор»
Теперь можно проводить процесс блестящего лужение. Используйте для этого представленный комплект:
Вернуться к подбору комплекта
Серебрение — Меди, латуни, бронзы
Перед серебрением меди, латуни или бронзы, необходимо сначала провести предварительную очистку и затем активацию металлической поверхности. Используйте для этого представленные составы:
- Состав «Универсальный очиститель»
- Состав «Химический активатор»
После этого, для повышения антикоррозионных свойств покрытия, перед проведением процесса серебрения, рекомендуется нанести на металлическую поверхность слой никеля. Используйте для этого представленный комплект:
Теперь можно проводить процесс блестящего серебрения. Используйте для этого представленный электролит:
Вернуться к подбору комплекта
Хромирование — Меди, латуни, бронзы
Перед хромированием меди, латуни или бронзы, необходимо сначала провести предварительную очистку и затем активацию металлической поверхности. Используйте для этого представленные составы:
- Состав «Универсальный очиститель»
- Состав «Химический активатор»
Для повышения блеска и износостойкости конечного покрытия, перед проведением процесса декоративного хромирования, на поверхность рекомендуется нанести промежуточный слой никеля. Используйте для этого любой из представленных комплектов:
- Комплект «Блестящий никель» (требуется источник питания)
- Комплект «Электролиз-никель» (не требуется источник питания)
После этого, можно проводить процесс декоративного хромирования. Используйте для этого любой из представленных комплектов:
или
Вернуться к подбору комплекта
Меднение — Хромированной поверхности
Блестящее декоративное хромирование представляет собой трехслойное металлическое покрытие состоящее из первичного слоя меди, наносимого на основу для повышения адгезионных и отражательных свойств покрытия, слоя никеля, используемого для повышения его антикоррозийных свойств, и конечного слоя хрома, использующегося в качестве блестящего декоративного покрытия, и обладающего именно в такой связке, одновременно и зеркальным блеском, и исключительными антикоррозионными свойствами. На поверхности хрома в обычных условиях имеется инертная оксидная пленка, которая при нанесении на него другого металлопокрытия не обеспечивает ему достаточного сцепления и поэтому, перед нанесением другого металлопокрытия, необходимо удалить весь слой хрома. Используйте для этого представленный состав:
После удаления слоя хрома, можно заметить металлическое покрытие, имеющее едва заметный желтоватый оттенок, это слой никеля. Перед проведением процесса блестящего меднения, его необходимо активировать. Используйте для этого представленный состав:
После этого, можно проводить процесс блестящего меднения. Используйте для этого представленный комплект:
Вернуться к подбору комплекта
Никелирование — Хромированной поверхности
Блестящее декоративное хромирование представляет собой трехслойное металлическое покрытие состоящее из первичного слоя меди, наносимого на основу для повышения адгезионных и отражательных свойств покрытия, слоя никеля, используемого для повышения его антикоррозийных свойств, и конечного слоя хрома, использующегося в качестве блестящего декоративного покрытия, и обладающего именно в такой связке, одновременно и зеркальным блеском, и исключительными антикоррозионными свойствами. На поверхности хрома в обычных условиях имеется инертная оксидная пленка, которая при нанесении на него другого металлопокрытия не обеспечивает ему достаточного сцепления и поэтому, перед нанесением другого металлопокрытия, необходимо удалить весь слой хрома. Используйте для этого представленный состав:
После удаления слоя хрома, можно заметить покрытие, имеющее едва заметный желтоватый оттенок, это слой никеля. Перед проведением процесса золочения, его необходимо активировать. Используйте для этого представленный состав:
После этого, можно проводить процесс блестящего никелирования. Используйте для этого представленный комплект:
Вернуться к подбору комплекта
Цинкование — Хромированной поверхности
Блестящее декоративное хромирование представляет собой трехслойное металлическое покрытие состоящее из первичного слоя меди, наносимого на основу для повышения адгезионных и отражательных свойств покрытия, слоя никеля, используемого для повышения его антикоррозийных свойств, и конечного слоя хрома, использующегося в качестве блестящего декоративного покрытия, и обладающего именно в такой связке, одновременно и зеркальным блеском, и исключительными антикоррозионными свойствами. На поверхности хрома в обычных условиях имеется инертная оксидная пленка, которая при нанесении на него другого металлопокрытия не обеспечивает ему достаточного сцепления и поэтому, перед нанесением другого металлопокрытия, необходимо удалить весь слой хрома. Используйте для этого представленный состав:
После удаления слоя хрома, можно заметить покрытие, имеющее едва заметный желтоватый оттенок, это слой никеля. Перед проведением процесса лужения, никелевое покрытие необходимо активировать. Используйте для этого представленный состав:
После этого, можно проводить процесс блестящего цинкования. Используйте для этого представленный комплект:
Вернуться к подбору комплекта
Анодирование — Не токопроводящих материалов
Используя данные процесс, можно анодировать только алюминиевую поверхность
Вернуться к подбору комплекта
Золочение — Не токопроводящих материалов
Нанесение металлического покрытия на не токопроводящие материалы является довольно трудоемким процессом. Для нанесения металлического покрытия сначала необходимо создать токопроводящий слой на поверхности детали. Используйте для этого любой из представленных комплектов:
После металлизации и нанесения химического медного покрытия, на поверхность изделия при малом токе наносится “затягивающее” медное покрытие. Используйте для этого представленный комплект:
После этого, для повышения антикоррозионных свойств покрытия, рекомендуется нанести на металлическую поверхность слой никеля. Используйте для этого любой из представленных комплектов:
Теперь можно проводить золочение. Используйте для этого представленный электролит:
Вернуться к подбору комплекта
Копи-хромирование — Не токопроводящих материалов
Нанесение металлического покрытия на не токопроводящие материалы является довольно трудоемким процессом. Для нанесения металлического покрытия сначала необходимо создать токопроводящий слой на поверхности детали. Используйте для этого представленный комплект:
После металлизации и нанесения химического медного покрытия, на поверхность при малом токе необходимо нанести “затягивающее” медное покрытие. Используйте для этого представленный комплект:
После этого можно наносить покрытие «КОПИ-ХРОМ». Используйте для этого представленный комплект:
Вернуться к подбору комплекта
Лужение — Не токопроводящих материалов
Нанесение металлического покрытия на не токопроводящие материалы является довольно трудоемким процессом. Для нанесения металлического покрытия сначала необходимо создать токопроводящий слой на поверхности детали. Используйте для этого представленный комплект:
После металлизации и нанесения химического медного покрытия, на поверхность при малом токе наносится “затягивающее” медное покрытие. Используйте для этого представленный комплект:
Теперь можно проводить процесс блестящего лужения. Используйте для этого представленный комплект:
Вернуться к подбору комплекта
Меднение — Не токопроводящих материалов
Нанесение металлического покрытия на не токопроводящие материалы является довольно трудоемким процессом. Для нанесения металлического покрытия сначала необходимо создать токопроводящий слой на поверхности детали. Используйте для этого представленный комплект:
После металлизации и нанесения химического медного покрытия, на поверхность при малом токе наносится “затягивающее” медное покрытие. Используйте для этого представленный комплект:
Вернуться к подбору комплекта
Никелирование — Не токопроводящих материалов
Нанесение металлического покрытия на не токопроводящие материалы является довольно трудоемким процессом. Для нанесения металлического покрытия сначала необходимо создать токопроводящий слой на поверхности детали. Используйте для этого представленный комплект:
После металлизации и нанесения химического медного покрытия, на поверхность при малом токе наносится “затягивающее” медное покрытие. Используйте для этого представленный комплект:
После этого можно проводить процесс блестящего никелирования. Используйте для этого представленный комплект:
Вернуться к подбору комплекта
Серебрение — Не токопроводящих материалов
Нанесение металлического покрытия на не токопроводящие материалы является довольно трудоемким процессом. Для нанесения металлического покрытия сначала необходимо создать токопроводящий слой на поверхности детали. Используйте для этого представленный комплект:
После металлизации и нанесения химического медного покрытия, на поверхность при малом токе необходимо нанести “затягивающее” медное покрытие. Используйте для этого представленный комплект:
После этого, для повышения антикоррозионных свойств покрытия, рекомендуется нанести на металлическую поверхность слой блестящего никеля. Используйте для этого представленный комплект:
Теперь можно проводить процесс блестящего серебрения. Используйте для этого представленный электролит:
Вернуться к подбору комплекта
Цинкование — Не токопроводящих материалов
Нанесение металлического покрытия на не токопроводящие материалы является довольно трудоемким процессом. Для нанесения металлического покрытия сначала необходимо создать токопроводящий слой на поверхности детали. Используйте для этого представленный комплект:
После металлизации и нанесения химического медного покрытия, на поверхность детали, при малом токе наносится “затягивающее” медное покрытие. Используйте для этого представленный комплект:
Теперь можно проводить процесс блестящего цинкования. Используйте для этого представленный комплект:
Вернуться к подбору комплекта
Хромирование — Не токопроводящих материалов
Нанесение металлического покрытия на не токопроводящие материлы является довольно трудоемким процессом. Для начала необходимо создать токопроводящий слой на поверхности детали. Используйте для этого представленный комплект:
После металлизации и нанесения химического медного покрытия, на поверхность при малом токе наносится “затягивающее” медное покрытие. Используйте для этого представленный комплект:
После этого на осажденное медное покрытие рекомендуется нанести слой никеля. Используйте для этого любой из представленных комплектов:
- Комплект «Блестящий никель» (требуется источник питания)
- Комплект «Электролиз-никель» (не требуется источник питания)
Теперь можно проводить процесс декоративного хромирования. Используйте для этого любой из представленных комплектов:
или
Вернуться к подбору комплекта
Золочение — Железа и стали
Перед золочением железа или стали, необходимо сначала провести очистку и затем активацию металлической поверхности. Используйте для этого представленные составы.
- Состав «Универсальный очиститель»
- Состав «Химический активатор»
После этого, для повышения отражательных и антикоррозионных свойств конечного покрытия, на металлическую поверхность наносится слой никеля. Используйте для никелирования любой из представленных комплектов:
Теперь можно проводить процесс золочения. Используйте для этого представленный электролит:
Вернуться к подбору комплекта
Копи-хромирование — Железа и стали
Перед нанесением покрытия «КОПИ-ХРОМ» на железо или сталь, необходимо сначала провести очистку и затем активацию металлической поверхности. Используйте для этого представленные составы.
- Состав «Универсальный очиститель»
- Состав «Химический активатор»
После этого для повышения блеска и износостойкости конечного покрытия, на металлическую поверхность рекомендуется нанести блестящее никелевое покрытие. Используйте для этого представленный комплект:
Теперь можно наносить покрытие «КОПИ-ХРОМ». Используйте для этого представленный комплект:
Вернуться к подбору комплекта
Меднение — Железа и стали
Перед нанесением меди на железо или сталь, необходимо сначала провести предварительную очистку и затем активацию металлической поверхности. Используйте для этого представленные составы:
- Состав «Универсальный очиститель»
- Состав «Химический активатор»
Теперь можно проводить процесс блестящего меднения. Используйте для этого представленный комплект:
Вернуться к подбору комплекта
Никелирование — Железа и стали
Перед никелированием железной или стальной поверхности, необходимо сначала провести предварительную очистку и затем активацию металлической поверхности. Используйте для этого представленные составы:
- Состав «Универсальный очиститель»
- Состав «Химический активатор»
После этого можно проводить процесс блестящего никелирования. Используйте для этого представленный комплект:
Вернуться к подбору комплекта
Серебрение — Железа и стали
Перед серебрением железа или стали необходимо сначала провести предварительную очистку и затем активацию металлической поверхности. Используйте для этого представленные составы:
- Состав «Универсальный очиститель»
- Состав «Химический активатор»
После этого, для повышения отражательных и антикоррозионных свойств конечного покрытия, нанесите на очищенную поверхность слой никеля. Используйте для этого представленный комплект:
Теперь можно проводить процесс блестящего серебрения. Используйте для этого представленный электролит:
Вернуться к подбору комплекта
Хромирование — Железа и стали
Перед хромированием железа или стали, необходимо сначала провести очистку и затем активацию металлической поверхности. Используйте для этого представленные составы.
- Состав «Универсальный очиститель»
- Состав «Химический активатор»
После этого, для повышения отражательных и антикоррозионных свойств конечного хромированного покрытия, на металлическую поверхность наносится слой никеля. Используйте для никелирования любой из представленных комплектов:
- Комплект «Блестящий никель» (требуется источник питания)
- Комплект «Электролиз-никель» (не требуется источник питания)
Теперь можно проводить процесс декоративного хромирования. Используйте для этого любой из представленных комплектов:
или
Вернуться к подбору комплекта
Анодирование — Легированной и закаленной стали
Используя данные процесс, можно анодировать только алюминиевую поверхность
Вернуться к подбору комплекта
Золочение — Легированной и закаленной стали
Перед золочением легированной или закаленной стали, необходимо сначала провести электрополировку стальной поверхности. Используйте для этого представленный комплект:
После этого, необходимо обработать поверхность детали в представленном составе:
Затем на поверхность наносится слой блестящего никеля. Используйте для этого представленный комплект:
После этого можно проводить процесс золочения. Используйте для этого представленный электролит:
Вернуться к подбору комплекта
Копи-хромирование — Легированной и закаленной стали
Перед нанесением покрытия «КОПИ-ХРОМ» на легированную или закаленную сталь, рекомендуется сначала провести электрополировку стальной поверхности. Используйте для этого представленный комплект:
После этого, необходимо обработать поверхность детали в представленном составе:
После этого для повышения блеска и износостойкости конечного покрытия, на металлическую поверхность рекомендуется нанести блестящее никелевое покрытие. Используйте для этого представленный комплект:
Теперь на металлическую поверхность можно наносить покрытие «КОПИ-ХРОМ». Используйте для этого представленный комплект:
Вернуться к подбору комплекта
Лужение — Легированной и закаленной стали
Перед лужением легированной или закаленной стали, необходимо сначала провести электрополировку стальной поверхности. Используйте для этого представленный комплект:
После этого необходимо обработать металлическую поверхность в представленном составе:
После этого можно проводить процесс блестящего лужения. Используйте для этого представленный комплект:
Вернуться к подбору комплекта
Меднение — Легированной и закаленной стали
Перед меднением легированной или закаленной стали, необходимо сначала провести электрополировку стальной поверхности. Электрополировка вытравливает тончайший слой металла, удаляет окисные отложения и придает металлической поверхности дополнительный блеск. Используйте для этого представленный комплект:
После этого, необходимо обработать деталь в активаторе для нержавеющей стали. Используйте для этого представленный состав:
После этого можно проводить процесс блестящего меднения. Используйте для этого представленный комплект:
Вернуться к подбору комплекта
Никелирование — Легированной и закаленной стали
Перед никелированием легированной или закаленной стали, рекомендуется сначала провести электрополировку стальной поверхности. Используйте для этого представленный комплект:
Затем необходимо обработать поверхность детали в представленном составе:
После этого можно проводить процесс блестящего никелирования. Используйте для этого представленный комплект:
Вернуться к подбору комплекта
Серебрение — Легированной и закаленной стали
Перед серебрением легированной или закаленной стали, необходимо сначала провести электрополировку стальной поверхности. Используйте для этого представленный комплект:
После этого, необходимо обработать поверхность детали в представленном составе:
Затем на поверхность наносится слой блестящего никеля. Используйте для этого представленный комплект:
Теперь можно проводить процесс блестящего серебрения. Используйте для этого представленный электролит:
Вернуться к подбору комплекта
Цинкование — Легированной и закаленной стали
Перед цинкованием легированной или закаленной стали, рекомендуется сначала провести электрополировку стальной поверхности. Используйте для этого представленный комплект:
После этого необходимо обработать поверхность детали в представленном составе:
После этого можно проводить процесс блестящего цинкования. Используйте для этого представленный комплект:
Вернуться к подбору комплекта
Хромирование — Легированной и закаленной стали
Перед хромированием легированной или закаленной стали, необходимо сначала провести электрополировку стальной поверхности. Используйте для этого представленный комплект:
После этого, необходимо активировать металлическую поверхность и нанести на нее слой никеля. Используйте для этого представленный состав:
Затем на поверхность наносится слой блестящего никеля. Используйте для этого представленный комплект:
Теперь можно проводить процесс декоративного хромирования. Используйте для этого любой из представленных комплектов:
или
Вернуться к подбору комплекта
Анодирование — Цинка, свинца, свинцовых сплавов
Используя данные процесс, можно анодировать только алюминиевую поверхность
Вернуться к подбору комплекта
Золочение — Цинка, свинца, свинцовых сплавов
Перед золочением цинка, свинца, медно-свинцовых или оловянно-свинцовых сплавов, необходимо сначала провести очистку и затем активацию металлической поверхности. Используйте для этого, представленные составы:
- Состав «Универсальный очиститель»
- Состав «Химический активатор»
После этого, на поверхность необходимо сначала нанести первичное медное покрытие. Электролит для первичного меднения имеет нейтральный уровень рН раствора, не разъедает поверхность деталей, сделанных из таких металлов и сплавов, и обеспечивает с ними отличное сцепление. Используйте для этого представленный комплект:
Несмотря на возможность напрямую наносить золото на покрытие первичная медь, мы рекомендуем нанести на него промежуточный слой никеля. Это повысит износостойкость и антикоррозионные свойства золотого покрытия. Используйте для никелирования любой из представленных комплектов:
После этого можно проводить процесс золочения. Используйте для этого представленный электролит:
Вернуться к подбору комплекта
Копи-хромирование — Цинка, свинца, свинцовых сплавов
Перед нанесением покрытия «КОПИ-ХРОМ» на цинк, свинец, медно-свинцовые или оловянно-свинцовые сплавы, необходимо сначала провести очистку и затем активацию металлической поверхности. Используйте для этого, представленные составы:
- Состав «Универсальный очиститель»
- Состав «Химический активатор»
После этого, на поверхность необходимо сначала нанести первичное медное покрытие. Электролит для первичного меднения имеет нейтральный уровень рН раствора, не разъедает поверхность деталей, сделанных из таких металлов и сплавов, и обеспечивает с ними отличное сцепление. Используйте для этого представленный комплект:
После этого, для повышения блеска и антикоррозионных свойств на металлическую поверхность рекомендуется нанести блестящее медное покрытие. Используйте для этого представленный комплект:
Теперь можно нанести покрытие «КОПИ-ХРОМ». Используйте для этого представленный комплект:
Вернуться к подбору комплекта
Лужение — Цинка, свинца, свинцовых сплавов
Перед лужением цинка, свинца, медно-свинцовых или оловянно-свинцовых сплавов, необходимо сначала провести очистку, затем активацию металлической поверхности. Используйте для этого, представленные составы:
- Состав «Универсальный очиститель»
- Состав «Химический активатор»
После этого, на поверхность необходимо сначала нанести первичное медное покрытие. Электролит для первичного меднения имеет нейтральный уровень рН раствора, не разъедает поверхность деталей, сделанных из таких металлов и сплавов, и обеспечивает с ними отличное сцепление. Используйте для этого представленный комплект:
Теперь можно проводить процесс блестящего лужения. Используйте для этого представленный комплект:
Вернуться к подбору комплекта
Меднение — Цинка, свинца, свинцовых сплавов
Перед меднением цинка, свинца, медно-свинцовых или оловянно-свинцовых сплавов, необходимо сначала провести очистку, затем активацию металлической поверхности. Используйте для этого, представленные составы:
- Состав «Универсальный очиститель»
- Состав «Химический активатор»
После этого, на поверхность необходимо сначала нанести первичное адгезионное медное покрытие. Электролит для первичного меднения имеет нейтральный уровень рН раствора, не разъедает поверхность деталей сделанных из таких металлов и сплавов и обеспечивает с ними отличное сцепление. Используйте для этого представленный комплект:
После этого можно проводить процесс блестящего меднения. Используйте для этого представленный комплект:
Вернуться к подбору комплекта
Никелирование — Цинка, свинца, свинцовых сплавов
Перед никелированием цинка, свинца, медно-свинцовых или оловянно-свинцовых сплавов, необходимо сначала провести очистку, затем активацию металлической поверхности. Используйте для этого, представленные составы:
- Состав «Универсальный очиститель»
- Состав «Химический активатор»
После этого, на поверхность необходимо сначала нанести первичное медное покрытие. Электролит для первичного меднения имеет нейтральный уровень рН раствора, не разъедает поверхность деталей, сделанных из таких металлов и сплавов, и обеспечивает с ними отличное сцепление. Используйте для этого представленный комплект:
Далее можно проводить процесс блестящего никелирования. Используйте для этого представленный комплект:
Вернуться к подбору комплекта
Серебрение — Цинка, свинца, свинцовых сплавов
Перед серебрением цинка, свинца, медно-свинцовых или оловянно-свинцовых сплавов, необходимо сначала провести очистку и затем активацию металлической поверхности. Используйте для этого представленные составы:
- Состав «Универсальный очиститель»
- Состав «Химический активатор»
После этого, на поверхность необходимо сначала нанести первичное медное покрытие. Электролит для первичного меднения имеет нейтральный уровень рН раствора, не разъедает поверхность деталей, сделанных из таких металлов и сплавов, и обеспечивает с ними отличное сцепление. Используйте для этого представленный комплект:
Несмотря на возможность напрямую наносить серебро на покрытие первичная медь, мы рекомендуем нанести на него промежуточный слой никеля. Это повысит блеск и износостойкость металлического покрытия. Используйте для этого представленный комплект:
Теперь можно проводить процесс блестящего серебрения. Используйте для этого представленный электролит:
Вернуться к подбору комплекта
Цинкование — Цинка, свинца, свинцовых сплавов
Перед нанесением блестящего цинкового покрытия на цинк, свинец, медно-свинцовые или оловянно-свинцовые сплавы, необходимо сначала провести очистку и затем активацию металлической поверхности. Используйте для этого, представленные составы:
- Состав «Универсальный очиститель»
- Состав «Химический активатор»
После этого, на поверхность необходимо сначала нанести первичное медное покрытие. Электролит для первичного меднения имеет нейтральный уровень рН раствора, не разъедает поверхность деталей, сделанных из таких металлов и сплавов, и обеспечивает с ними отличное сцепление. Используйте для этого представленный комплект:
Теперь можно проводить процесс блестящего цинкования. Используйте для этого представленный комплект:
Вернуться к подбору комплекта
Хромирование — Цинка, свинца, свинцовых сплавов
Перед хромированием цинка, свинца, медно-свинцовых или оловянно-свинцовых сплавов, необходимо сначала провести очистку, затем активацию металлической поверхности. Используйте для этого, представленные составы:
- Состав «Универсальный очиститель»
- Состав «Химический активатор»
После этого, на поверхность необходимо сначала нанести первичное медное покрытие. Электролит для первичного меднения имеет нейтральный уровень рН раствора, не разъедает поверхность деталей, сделанных из таких металлов и сплавов и обеспечивает с ними отличное сцепление. Используйте для этого представленный комплект:
Несмотря на возможность напрямую наносить хром на покрытие первичная медь, мы рекомендуем нанести на него промежуточный слой никеля. Это повысит износостойкость и антикоррозионные свойства золотого покрытия. Используйте для никелирования любой из представленных комплектов:
- Комплект «Блестящий никель» (требуется источник тока)
- Комплект «Электролиз-никель» (не требуется источник тока)
Теперь можно проводить процесс декоративного хромирования. Используйте для этого любой из представленных комплектов:
или
Вернуться к подбору комплекта
Золочение — Никеля
Можно сразу наносить золото на никелевую поверхность. Перед золочением рекомендуется только обработать деталь в растворе химического активатора. Используйте для этого представленный состав:
Теперь можно проводить процесс золочения. Используйте для этого представленный электролит:
Вернуться к подбору комплекта
Копи-хромирование — Никеля
Можно сразу наносить покрытие «КОПИ-ХРОМ» на никель. Перед нанесением покрытия необходимо только обработать деталь в растворе химического активатора. Используйте для этого представленный состав:
Теперь можно наносить покрытие «КОПИ-ХРОМ». Используйте для этого представленный комплект:
Вернуться к подбору комплекта
Лужение — Никеля
Перед лужением никелевой поверхности, необходимо только провести активацию металлической поверхности. Используйте для этого представленный состав:
После этого, можно проводить процесс блестящего лужения. Используйте для этого представленный комплект:
Вернуться к подбору комплекта
Никелирование — Никеля
Можно сразу наносить никель на никелевую поверхность. Перед никелированием рекомендуется только обработать деталь в растворе химического активатора. Используйте для этого представленный состав:
Теперь можно проводить процесс блестящего никелирования. Используйте для этого представленный комплект:
Вернуться к подбору комплекта
Серебрение — Никеля
Можно сразу серебрить никелевую поверхность. Перед серебрением рекомендуется только обработать деталь в растворе химического активатора. Используйте для этого представленный состав:
Теперь можно проводить процесс блестящего серебрения. Используйте для этого представленный электролит:
Вернуться к подбору комплекта
Цинкование — Никеля
Перед нанесением блестящего цинкового покрытия на никель, необходимо провести активацию металлической поверхности. Используйте для этого представленный состав:
После этого можно проводить процесс блестящего цинкования. Используйте для этого представленный комплект:
Вернуться к подбору комплекта
Хромирование — Никеля
Можно сразу осаждать хром на никелевую поверхность. Перед хромированием рекомендуется только обработать деталь в растворе химического активатора. Используйте для этого представленный состав:
Теперь можно проводить процесс декоративного хромирования. Используйте для этого любой из представленных комплектов:
или
Вернуться к подбору комплекта
Копи-хромирование — Олова
Перед нанесением покрытия «КОПИ-ХРОМ» на олово, необходимо сначала провести предварительную очистку и затем активацию металлической поверхности. Используйте для этого представленные составы:
- Состав «Универсальный очиститель»
- Состав «Химический активатор»
После этого можно наносить покрытие «КОПИ-ХРОМ». Используйте для этого представленный комплект:
Вернуться к подбору комплекта
Лужение — Олова
Перед нанесением олова на оловянную поверхность, необходимо сначала провести предварительную очистку и затем активацию металлической поверхности. Используйте для этого представленные составы:
- Состав «Универсальный очиститель»
- Состав «Химический активатор»
Теперь можно проводить процесс блестящего лужения. Используйте для этого представленный комплект:
Вернуться к подбору комплекта
Меднение — Олова
Перед нанесением меди на оловянную поверхность, необходимо сначала провести предварительную очистку и затем активацию металлической поверхности. Используйте для этого представленные составы:
- Состав «Универсальный очиститель»
- Состав «Химический активатор»
Теперь можно проводить процесс блестящего меднения. Используйте для этого представленный комплект:
Вернуться к подбору комплекта
Цинкование — Олова
Перед нанесением блестящего цинкового покрытия на олово, необходимо сначала провести предварительную очистку и затем активацию металлической поверхности. Используйте для этого представленные составы:
- Состав «Универсальный очиститель»
- Состав «Химический активатор»
Теперь можно проводить процесс блестящего цинкования. Используйте для этого представленный комплект:
Вернуться к подбору комплекта
Хромирование — Олова
Перед хромированием олова, необходимо сначала провести предварительную очистку и затем активацию металлической поверхности. Используйте для этого представленные составы:
- Состав «Универсальный очиститель»
- Состав «Химический активатор»
Несмотря на возможность напрямую наносить хром на олово, мы рекомендуем нанести на него промежуточный слой никеля. Это повысит износостойкость и антикоррозионные свойства покрытия. Используйте для никелирования любой из представленных комплектов:
- Комплект «Блестящий никель» (требуется источник тока)
- Комплект «Электролиз-никель» (не требуется источник тока)
Теперь можно проводить процесс декоративного хромирования. Используйте для этого любой из представленных комплектов:
или
Вернуться к подбору комплекта
Золочение — Золота
Для нанесения слоя золота на позолоченную поверхность необходимо только провести активацию металлической поверхности. Используйте для этого представленный состав:
После этого можно проводить процесс золочения. Используйте для этого представленный электролит:
Вернуться к подбору комплекта
Копи-хромирование — Золота
Для нанесения покрытия «КОПИ-ХРОМ» на золото или позолоченную поверхность необходимо только провести активацию поверхности детали. Используйте для этого представленный состав:
Теперь можно наносить покрытие «КОПИ-ХРОМ». Используйте для этого представленный комплект:
Вернуться к подбору комплекта
Лужение — Золота
Для нанесения слоя олова на золото или позолоченную поверхность необходимо только провести активацию металлической поверхности. Используйте для этого представленный состав:
Теперь можно проводить процесс блестящего лужения. Используйте для этого представленный комплект:
Вернуться к подбору комплекта
Меднение — Золота
Для нанесения блестящего медного покрытия на золото или на позолоченную поверхность необходимо сначала провести процесс химической активации. Используйте для этого представленный состав:
Теперь можно проводить процесс блестящего меднения. Используйте для этого представленный комплект:
Вернуться к подбору комплекта
Никелирование — Золота
Для нанесения никеля на золото или позолоченную поверхность необходимо только провести активацию металлической поверхности. Используйте для этого представленный состав:
Теперь можно проводить процесс блестящего никелирования. Используйте для этого представленный комплект:
Вернуться к подбору комплекта
Серебрение — Золота
Перед серебрением золота или позолоченной поверхности необходимо провести только активацию металлической поверхности. Используйте для этого представленный состав:
Теперь можно проводить процесс блестящего серебрения. Используйте для этого представленный электролит:
Вернуться к подбору комплекта
Цинкование — Золота
Перед нанесением блестящего цинкового покрытия на золото необходимо провести только активацию металлической поверхности. Используйте для этого представленный состав:
Теперь можно проводить процесс блестящего цинкования. Используйте для этого представленный комплект:
Вернуться к подбору комплекта
Хромирование — Золота
Для нанесения блестящего декоративного хрома на золото, необходимо провести активацию металлической поверхности. Используйте для этого представленный состав:
Теперь можно проводить процесс декоративного хромирования. Используйте для этого любой из представленных комплектов:
или
Вернуться к подбору комплекта
Технология и механизм лужения: оловянирование, сплав олово-висмут.
1. Что такое олово и висмут?
Олово — мягкий металл серебристо-белого цвета. Плотность 7,28 г/см3, температура плавления 232°С, атомная масса 118,7 г/моль. В атмосферных условиях, даже в присутствии влаги, олово окисляется медленно. Разбавленные растворы минеральных кислот при комнатной температуре практически не растворяют олово, оно растворяется в концентрированных серной и соляной кислотах при нагревании. В растворах едкой щелочи олово неустойчиво и при нагревании растворяется с образованием станнатов. С органическими кислотами олово образует комплексные соединения, причем потенциал олова становится более отрицательным, чем потенциал железа, т.е. олово становится анодным покрытием.
Коррозионная стойкость олова в зависимости от рН приведена на рисунке 1. Видно, что олово наиболее устойчиво в диапазне рН от 6 до 9.
Рисунок 1 — Зависимость скорости коррозии олова от величины рН среды.
Висмут — в нормальных условиях блестящий серебристо-белый металл. Плотность 9,747 г/см³ температура плавления 271,35 °C, атомная масса 208,98 г/моль. В соединениях висмут проявляет степени окисления -3, +1, +2, +3, +4, +5. При комнатной температуре в среде сухого воздуха не окисляется, но в среде влажного воздуха покрывается тонкой плёнкой оксида. С металлами способен образовывать интерметаллиды — висмутиды.
Олово-висмутовое покрытие нашло самое широкое применение в радиоэлектронике и электротехнике. Чаще всего оловом покрываются токоведущие медные и алюминиевые шины, электроконтакты, корпуса приборов, крепеж из нержавеющей стали, контактирующий с алюминием (рисунок 2,3).
Рисунок 2 — Примеры оловянированных медных шин.
Рисунок 3 — Примеры оловянированных корпусных деталей.
Чисто оловянные покрытия просты в получении, но имеют ряд существенных недостатков:
(более подробно о некоторых из них написано в статье)
• При хранении оловянных покрытий характерен рост на их поверхности нитевидных кристаллов, длина которых может достигать величины 5-10 мм (рисунок 4). Нитевидные кристаллы вызывают короткие замыкания при эксплуатации плотно расположенной электрорадиотехнической аппаратуры. Причины возникновения подобных несовершенств покрытия еще недостаточно изучены. Установлено, что на образование усов в значительной степени влияет материал катода. Основной причиной считается наличие внутренних напряжений сжатия в покрытии, которые возникают под влиянием осаждения некоторых примесей, инородных включений, диффузии компонентов основы в покрытие, напряжений в материале основы. На оловянном покрытии, нанесенном на латунь, медь и цинк нитевидные кристаллы появляются чаще и растут быстрее, чем на стальной основе. Применение никелевого подслоя тормозит этот процесс.
Рисунок 4 — «Усы» на олове.
• Олово является полиморфным металлом. В обычных условиях оно существует в виде β-модификации (белое олово), устойчивой выше 13,2 °C. При низких температурах белое олово переходит в другую аллотропную модификацию (серое олово). Переход сопровождается увеличением удельного объема, что приводит к разрушению оловянного покрытия. Это явление получило название «оловянная чума» (рисунок 5).
Рисунок 5 — Оловянный стержень, пораженный «оловянной чумой».
• Чисто оловянные покрытия имеют очень короткий срок эксплуатации в качестве покрытия под пайку. Практика показывает, что паяемость оловянного покрытия иногда ухудшается в течение 2-3 суток. Неблагоприятно сказывается значительная пористость покрытия, наличие в покрытии примесей некоторых металлов, которые включаются в процессе электрокристаллизации или в результате диффузии компонентов металла основы, например цинка из латуни. Так же паяемость луженой поверхности может уменьшаться вследствие образования на границе медь-олово интерметаллических соединений типа Cu3Sn, Cu6Sn5, которые при толщине меньше 3 мкм теряют пластичность.
Все эти недостатки устраняются при введении в олово висмута.
Диаграмма состояния сплава олово-всимут приведена на рисунке 6. Однако, стоит заметить, что гальванические сплавы олово-висмут легируются висмутом всего на десятые доли процента — этого уже достаточно для модификации свойств покрытия.
Рисунок 6 — Диаграмма состояния олово-висмут.
Для осаждения олова и его сплавов используют различные по природе электролиты, основными являются кислые и щелочные.
2. Механизм оловянирования и структура покрытия.2.1 Осаждение индивидуального олова из сернокислого электролита без ПАВ.
К кислым электролитам оловянирования относятся сульфатные, пирофосфатные, фенолсульфоновые, борфтористоводородные и др.
Самым популярным является сульфатный, состоящий из сульфата олова (II) и серной кислоты. Также могут вводиться добавки коллоидов и поверхностно — активных веществ. Общей чертой всех кислых ванн является то, что ионы Sn4+ всегда являются вредной примесью.
Сульфатная ванна может работать на достаточно высоких плотностях тока с выходом по току 80-90 %.
Серную кислоту вводят в электролит для снижения гидролиза оловянных солей, а также для предотвращения окисления двухвалентного олова в четырехвалентное и образования шероховатых осадков. При отсутствии органических веществ в кислых электролитах невозможно получить приемлемые осадки олова из-за образования крупных кристаллов и усиленного роста дендритов на краях деталей.
При отсутствии добавок в сульфатном электролите катодная поляризация весьма незначительна (рисунок 7).
Рисунок 7 — Катодная поляризационная кривая осаждения олова из сернокислого электролита без добавок при скорости развертки 1 мВ/сек.
По рисунку 7 кривую восстановления олова можно разделить на четыре части.
В области AB плотность тока близка к нулю, реакции нет. На области BC плотность тока возрастает от 0 до 39,8 мА/см2, что соответствует процессу восстановления олова. Участок CD характеризует площадку предельного диффузионного тока, которая начинается с некторой «просадки». Она объясняется тем, что на участке CD диффузия ионов олова из объема электролита к поверхности катода становится недостаточной. В области DE плотность тока увеличивается резко выше -0,46 В, что указывает на начало выделения водорода по реакции:
2H+ + 2e → H2
Исходя из результатов циклической вольтамперометрии (рисунок 8) восстановление олова из сернокислого электролита протекает в одну стадию (один пик восстановления а):
Sn2+ + 2e → Sn
Электроосаждение олова начинается при потенциале зарождения -0,43 В. При развертке в обратном направлении наблюдается один пик окисления а’ при -0,36 В. Это подтверждает одностадийность и анодного процесса.
Рисунок 8 — Циклическая вольт-амперограмма осаждения олова из сернокислого электролита без добавок при скорости развертки 10 мВ/сек.
По результатам электрохимической импедансной спектроскопии в ванне сернокислого оловянирования без добавок при -0,43В (рисунок 9) можно заключить, что восстановление олова контролируется и кинетически и диффузионно, так как импеданс Варбурга происходит в низкочастотном диапазоне.
Рисунок 9 — Результаты электрохимической импедансной спектроскопии в ванне сернокислого оловянирования без добавок при -0,43В.
Следует заметить, что в сульфатном растворе происходит окисление двухвалентного олова с последующим гидролизом:
SnSO4 + H2SO4 + 0.5O2 → Sn(SO4)2 + H2O
Sn(SO4)2 + 3H2O = 2H2SO4 + H2SnO3 ↓
Изменение концентрации сульфата олова в пределах 30-60 г/л не сказывается заметно на характере катодного процесса. Пониженная концентрация сульфата олова снижает максимальный предел рабочей плотности тока. При повышенном содержании сульфата олова аноды склонны к пассивированию.
Серная кислота повышает электропроводность электролита, предохраняет электролит от гидролиза и появления шероховатости на осадках. Концентрация серной кислоты может колебаться в пределах от 20 до 100 г/л. При малых концентрациях кислоты увеличивается опасность гидролиза и окисления сульфата олова, слишком большая ее концентрация приводит к снижению выхода но току, быстрому разрушению коллоидных добавок и пассивированию анодов.
Режим электролиза плотность тока и температура — в значительной степени влияет на качество осадков. При малых плотностях получаются осадки с крупнокристаллической структурой, отличающиеся повышенной пористостью. Чрезмерно высокая плотность тока приводит к тому, что осадки становятся шероховатыми, на краях растут дендриты. Для тонких покрытий (около 1-2 мкм) допустимы большие плотности, чем для толстых покрытий. Повышение температуры в период работы с сульфатными электролитами приводит к снижению катодной поляризации, уменьшению рассеивающей способности, ухудшению качества осадков.
Структура олова, полученного из сульфатной ванны без ПАВ стержневидная (рисунок 10).
Рисунок 10 — Микроизбражения осадков олова (SEM), полученных из сернокислого электролита без добавок при плотности тока 30 мА/см2 и температуре 25о С.
2.2 Осаждение индивидуального олова из сернокислого электролита с введением ПАВ.
Блестящие покрытия менее пористы и дольше сохраняют способность к пайке, поэтому даже при осаждении сплава олово-висмут им отдают предпочтение.
Введение в электролит ПАВ всегда увеличивает катодную поляризацию. Так, при добавлении крезолсульфоновой кислоты или смеси со столярным клеем катодная поляризация достигает 500-600 мВ. На рисунке 11 показаны примеры катодных кривых осаждения олова из сульфатного электролита при введении трех разных ПАВ, а на рисунке 12 — при введении этих ПАВ в смеси друг с другом.
Рисунок 11 — Катодные поляризационная кривые осаждения олова из сернокислого электролита с тремя различными ПАВ.
Рисунок 12 — Катодные поляризационные кривые осаждения олова из сернокислого электролита без ПАВ и со смешанными ПАВ.
Сульфатные электролиты оловянирования с добавкой ПАВ отличаются сравнительно высокой рассеивающей способностью, приближающейся к рассеивающей способности медных цианистых электролитов. Выход по току сульфатных оловянных электролитов с ПАВ равен примерно 90-98 %.
Структура осадков олова при введении ПАВ в электролиты выравнивается, зерно измельчается (рисунок 13). Это свидетельствует об увеличении скорости зарождения зерен и торможении скорости их роста, что вполне закономерно.
Рисунок 13 — Микроизображения осадков олова (SEM), полученных из сернокислого электролита с примененим смешанных ПАВ при плотности тока 30 мА/см2 и температуре 25о С.
Результаты рентгено-структурного анализа оловянного покрытия, полученного из электролита со смешанными ПАВ приведены на рисунке 14.
Рисунок 14 — Рентгенограмма олова, полученного из сернокислого электролита со смешанными ПАВ.
Разница в интенсивности дифракционного отражения граней кристаллов между покрытием и стандартным оловом с объемно-центрированной кубической решеткой приведена в таблице ниже.
Образец |
I(200) |
I(101) |
I(211) |
I(112) |
I(321) |
Покрытие |
8,6 |
34,1 |
9,2 |
100 |
7,2 |
Стандартное олово |
100,0 |
90,0 |
74,0 |
23,0 |
20,0 |
В покрытии самым интенсивным является отражение от грани (112).
Микроизображение поперечного излома оловянного покрытия приведено на рисунке 15.
Рисунок 15 — Микроизображение излома оловянного покрытия.
Осадки блестящего олова очень чувствительны к механическим загрязнениям, которые могут попадать в электролит из шлама, образующегося в результате окисления Sn2-. Нерастворимый осадок, содержащий ионы четырехвалентного олова, является коллоидным, легко проходит через любые фильтры.
2.3 Осаждение сплава олова-висмут из сернокислого электролита.
Электролиты осаждения сплава олово-висмут представляют собой обычные электролиты лужения с добавками небольших количеств солей висмута.
Добавка висмута к олову замедляет рост нитевидных кристаллов и предотвращает переход белого олова в рыхлое серое при низких температурах. Сплавы олова с висмутом образуют системы эвтектического типа, причем при содержании висмута до 5% предполагается образование твердого раствора устойчивого при температуре до 231,8°С. Так как с антикоррозионной точки зрения твердые растворы представляют наибольший интерес, и для предотвращения перехода белого олова в серое требуются очень малые количества висмута, подбирались такие условия электролиза при которых содержание висмута в сплаве не превышало бы 5%.
Электроосаждение сплавов представляет собой один из частых случаев протекания параллельных электрохимических процессов, причем при сплавообразовании они не всегда являются независимыми. Во многих случаях наблюдается их взаимное влияние (деполяризация или сверхполяризация). Кинетические кривые осаждения сплава олово-висмут из кислого электролита с ПАВ приведены на рисунке 16.
Рисунок 16 — Кинетические кривые осаждения сплава олово-висмут из кислого электролита с ПАВ. 1 — Сплав олово-висмут при температуре 40о С, 2 — то же при температуре 22о С, 3 — чистое олово при температуре 22о С, чистый висмут при температуре 22о С.
Видно, что при осаждении сплава наблюдается деполяризация, а выделение обоих компонентов происходит уже при небольших плотностях тока.
Микроструктура сплава олово-висмут, осажденного из кислого электролита с ПАВ, в зависимости от плотности тока, приведена на рисунке 17.
Рисунок 17 — Микрофотографии сплава олово-висмут, нанесенного на ковар из кислого электролита с ПАВ. Увеличение х500. Катодная плотность тока А/дм2: А — 0,1 Б — 0,5 В — 0,8.
Видно, что с ростом плотности тока зерно осадка измельчается.
Пример стальных деталей с олово-висмутовым блестящим покрытием приведен на рисунке 18.
Рисунок 18 — Пример деталей с олово-висмутовым блестящим покрытием.
Щелочные станнатные электролиты непригодны для получения этих сплавов, так как соли висмута в щелочной среде неустойчивы, и легко выпадают с образованием основных нерастворимых солей.
Висмут может вытесняться оловом из раствора по реакции:
3Sn + 2Bi3+ → 2Sn2+ + 2Bi
2.4 Механизм оловянирования из других кислых электролитов.
В пирофосфатных электролитах олово находится в виде комплексного аниона [Sn(P2О7)2]6-, что обусловливает хорошую рассеивающую способность электролитов и возможность замены щелочных электролитов, где скорость осаждения вдвое ниже и условия работы на ваннах более сложные. В пирофосфатном электролите, не содержащем ионов хлора и органических добавок, выделение на катоде компактных осадков при небольшой плотности тока происходит без заметной поляризации.
Основными компонентами фенолсульфонового электролита оловянирования являются сульфат олова и фенолсульфоновая кислота. При смешивании этих компонентов в воде образуется фенолсульфонат олова:
SnSO4 + 2C6H4OHSO3H → Sn(C6H4OHSO3)2 + H2SO4
Эти электролиты менее склонны к окислению, чем сульфатные.
Борфтористоводородные электролиты содержат оловянную соль борфтористоводородной кислоты (олово находится в двухвалентном состоянии), свободную HBF4, и H3BO3 или несколько органических ПАВ, без которых невозможно получить качественный осадок. Борфтористоводородные электролиты применяют при температурах от 20 до 40°С. Они позволяют применять более высокие плотности тока, по сравнению с сернокислыми электролитами. Максимальная допустимая плотность тока, при покрытии в стационарных ваннах 10-12 А/дм2. Аноды применяются чистые оловянные, анодная плотность тока примерно равна катодной. При рабочей плотности тока в 4-5 А/ дм2, выходы по току на катоде и на аноде составят 95-96 %. Для предупреждения окисления двухвалентного олова, и накопления четырехвалентного олова, в электролит рекомендуется вводить 3-5 мл гидразина.
2.5 Механизм щелочного оловянирования.
В щелочных электролитах олово находится в четырехвалентной форме в виде аниона SnO32-. Осаждение олова на катоде происходит по реакции:
SnO32- + 3H2О + 4е → Sn + 6ОН—
Щелочные электролиты обладают хорошей рассеивающей способностью и позволяют получать весьма равномерные покрытия на сложнорельефных деталях даже в том случае, когда они покрываются в барабанах.
Особо вредной примесью в щелочном электролите оловянирования является станнит-ион Sn(OH)2-4, где олово находится в двухвалентном состоянии. Присутствие в электролите даже незначительного количества двухвалентного олова приводит к образованию на катоде губчатого осадка, так как станнит-ионы восстанавливаются при небольшой поляризации и, следовательно, преимущественно перед станнат-ионами. Поскольку концентрация станнит-ионов очень мала, то уже вскоре после начала электролиза их разряд протекает на предельном токе диффузии. Вследствие этого на всей поверхности катода начинают образовываться микродендриты, на которых продолжает осаждаться рыхлый металл. Ввиду того, что на анодах двухвалентное олово будет образовываться в первую очередь, преимущественно перед четырехвалентным оловом, применяется частичная пассивация анодов.
2.4 Анодный процесс при лужении.
Анодный процесс подробно рассмотрен в статье.
Данная статья является интеллектуальной собственностью ООО «НПП Электрохимия» Любое копирование без прямой ссылки на сайт www.zctc.ru преследуется по закону. Текст статьи обработан сервисом Яндекс «Оригинальные тексты»
| Навигация по справочнику TehTab.ru: главная страница / / Техническая информация / / Химический справочник / / Водные растворы и смеси для обработки металлов.![]()
| |||||||||||||||||||||||||||||||||||||||||||||||||||||||||||||||||||||||||||||||||||||||||||||||||||||||||||||||||||||||||||||||||||||||||||
Нашли ошибку? Есть дополнения? Напишите нам об этом, указав ссылку на страницу.![]() | ||||||||||||||||||||||||||||||||||||||||||||||||||||||||||||||||||||||||||||||||||||||||||||||||||||||||||||||||||||||||||||||||||||||||||||
TehTab.ru Реклама, сотрудничество: [email protected] | Обращаем ваше внимание на то, что данный интернет-сайт носит исключительно информационный характер. Информация, представленная на сайте, не является официальной и предоставлена только в целях ознакомления. Все риски за использование информаци с сайта посетители берут на себя. Проект TehTab.ru является некоммерческим, не поддерживается никакими политическими партиями и иностранными организациями. |
Флагман новых технологий — Энергетика и промышленность России — № 4 (68) апрель 2006 года — WWW.EPRUSSIA.RU
Газета «Энергетика и промышленность России» | № 4 (68) апрель 2006 года
В марте в ООО «Севморкабель», входящем в ОАО «Севкабель-Холдинг», была введена в эксплуатацию линия гальванического лужения производства компании «Niehoff». Освоив данное производство, «Севкабель-Холдинг» станет первым российским производителем кабелей в резиновой изоляции с медной токопроводящей жилой, луженной оловом электролитическим способом.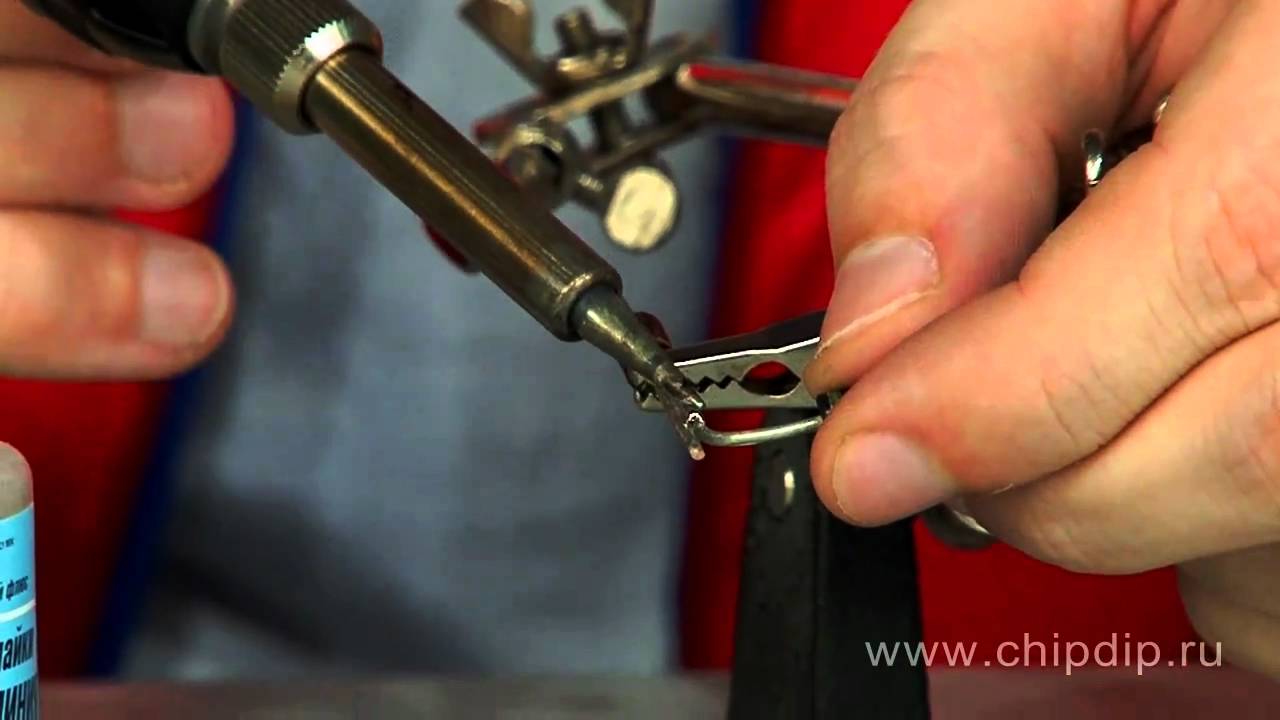
Введение в эксплуатацию данной линии является очередным этапом в рамках реализации проекта по выпуску кабелей в резиновой изоляции, в том числе судовых кабелей с изоляцией из полиэтилена и поливинилхлорида.
Данное оборудование уникально – всего в мире таких линий пять. ОАО «Севкабель-Холдинг» является единственным предприятием на территории России и СНГ, имеющим в своем производстве линию гальванического лужения. Сегодня на всех кабельных заводах России используется устаревшая технология лужения методом расплава олова и нанесения его на проволоку. Данный метод имеет ряд недостатков, основные из которых – неравномерная площадь покрытия проволоки оловом, что не всегда удовлетворяет техническим условиям ТУ 16‑505.850‑75, а также неэффективный расход олова.
На Западе же давно используется технология лужения при помощи электростатического осаждения олова на проволоку, что обеспечивает равномерное и более качественное покрытие по всей длине проволоки. При использовании данного метода лужения существенно повышается коррозийностойкость экрана и токопроводящей жилы и снижается интенсивность старения изоляции.
Таким образом, освоив данное производство, ОАО «Севкабель-Холдинг» станет первым российским производителем кабелей в резиновой изоляции, выполненных с применением операции лужения электролитическим способом.
Установленная линия гальванического лужения WPT.400. SN.1.4000 предназначена для непрерывного электролитического лужения проволоки из меди в соответствии со спецификацией и техническими данными. В линии происходит непрерывное осаждение олова электролитическим путем, при этом на волоченой или волоченой и отожженной медной проволоке получаются мелкокристаллические, прочно сцепленные с ней слои олова. Олово для осаждения покрытия вводится в ванну установки в виде литых анодов или окатышей, помещенных в корзины.
В качестве лудильного раствора используется высокоэффективный электролит, в который для лучшего осаждения вводятся в небольших количествах специальные присадки. Скорость движения проволоки и толщина слоя задаются как параметры заранее при помощи регулировок на пульте управления. Скорость движения проволоки достигает 15 м/с (900 м/мин.) Проволока перемещается через установку с заранее заданной скоростью приводом питающих валков. Схема электронного регулирования с интегратором заданных значений осуществляет плавный разгон или торможение установки во время ее пуска и останова.
Постоянный ток, соответствующий настройке на пульте управления и текущей скорости движения проволоки, создается при помощи выпрямителя. Благодаря постоянному согласованию тока и скорости движения проволоки гарантируется осаждение слоя постоянной толщины.
Во время останова установки для смены катушек либо при изменении скорости движения проволоки происходит автоматическое согласование тока, создаваемого выпрямителем, с тем, чтобы не возникло никакого неблагоприятного влияния на толщину слоя олова и проволоку.
Отсутствие дефектов в процессе лужения достигается за счет тщательной предварительной и последующей обработки проволоки в специальной химической части установки.
Вся установка в целом полностью герметизирована, так что никакие вредные или агрессивные газы не могут попасть в окружающую среду. Кроме того, установка работает под небольшим разрежением. Для этого воздух непрерывно отсасывается из нее установленным вентилятором и подается в газоочиститель. Вредные вещества, содержащиеся в воздухе, абсорбируются в нем водой. В качестве абсорбента используется пресная вода.
Пройдя промывочный колокол, отработанный воздух выводится в атмосферу через вытяжную трубу. Концентрация вредных веществ в отводимом отработанном воздухе отвечает нормам ЕС.
Промывочная вода, накапливающаяся в установке для лужения проволоки, собирается в коллекторе отработанной воды и подается из него в вакуумный испаритель, а затем улавливается коллектором дистиллята. Из него дистиллят перекачивается насосом обратно в установку.
Вся установка находится в кислотостойкой чаше, так что никакие опасные вещества не могут попасть в окружающую среду.
Установка работает от свободно программируемой системы управления. Кроме того, она снабжена соответствующими блокировками и защитными системами с тем, чтобы исключить угрозы для обслуживающего персонала.
Термин | Определение | |
ОБЩИЕ ПОНЯТИЯ | ||
1. Пайка Ндп. Напайка Спайка Припайка D. Е. Brazing; Soldering | Образование неразъемного соединения с межатомными связями путем нагрева соединяемых материалов ниже температуры их плавления, их смачивания припоем (см. пп.5 и 18), затекания припоя в зазор (см. п.17) и последующей его кристаллизации | |
2. Ндп. Обслуживание D. Verzinnen Е. Tinning | Образование на поверхности материала металлического слоя путем плавления припоя, смачивания припоем поверхности и последующей его кристаллизации | |
3. Паяное соединение D: Lotverbindung Е. Brazed (soldered) joint | Соединение, образованное пайкой | |
4. Паяемый материал | Основной материал заготовок или изделий, соединяемых пайкой или подвергаемых лужению. Примечание. Основной материал и заготовка — по ГОСТ 3.1109-82 | |
5. Припой D. Lot Е. Brazing alloy; Solder | Материал для пайки и лужения с температурой плавления ниже температуры плавления паяемых материалов | |
6. D. Hilfsmaterial Е. Auxiliary material | По ГОСТ 3.1109-82 Примечание. К вспомогательным материалам относятся: паяльные флюсы, вещества, ограничивающие растекание припоя и т.п. | |
7. Паяльный флюс Флюс Е. F. Flux | Вспомогательный материал, применяемый для удаления окислов с поверхности паяемого материала и припоя и предотвращения их образования. Примечание. Флюс может участвовать в образовании припоя путем выделения из него компонентов, разлагающихся при пайке металла | |
8. Полуда | Металлический слой на поверхности материала, образованный при лужении | |
9. Технологическое покрытие | Металлическое покрытие на паяемом материале, применяемое для защиты его от окисления при нагреве, участвующее в контактном плавлении и растворяющееся в расплавленном припое | |
10. D. Barrieruberzug Е. Barrier coating | Металлическое покрытие на паяемом материале, применяемое для предотвращения контакта материала с припоем или растекания припоя (см. п.16) на поверхность, не подлежащую пайке (лужению) и не растворяющееся или частично растворяющееся в расплавленном припое | |
11. Распайка Ндп. Распай Распаивание D. Е. Unbrazing; Unsoldering | Разъединение паяного соединения при нагреве его выше температуры начала плавления материала паяного шва (см. п.97) | |
12. Подпайка | Повторный нагрев паяного соединения и введение новой порции припоя с целью устранения дефектов | |
13. Перепайка D. Е. Rebrazing; Resoldering | Распайка и повторная пайка | |
14. Сборочный зазор под пайку Сборочный зазор D. Lotspalt bei Raumtemperatur Е. Cold clearance | Зазор между поверхностями паяемых заготовок или изделий, устанавливаемый при сборке | |
15. Паяльный зазор D. Lotspalt bei Lottemperatur Е. Hot clearance | Зазор между поверхностями паяемых заготовок или изделий, образующийся при температуре пайки | |
16. Растекание припоя Растекание D. Ausbreinten Е. Spreading | Распространение расплавленного припоя на поверхности паяемого материала | |
17. Затекание D. Е. Flowing | Заполнение расплавленным припоем паяльного зазора | |
18. Смачивание припоем Смачивание D. Benetztn Е. Wetting | Физико-химическое взаимодействие расплавленного припоя с паяемым материалом, проявляющееся в растекании припоя или образовании мениска с конечным краевым углом смачивания (см. п.24) | |
19. Десмачивание паяемого материала Десмачивание D. Entbenetzen Е. Dewetting | Увеличение краевого угла смачивания или уменьшение площади растекания припоя (см. п.23) при пайке или лужении по сравнению с их первоначально достигнутыми значениями. Примечания: 1. Десмачивание является следствием химического взаимодействия расплавленного припоя с паяемым материалом и изменения во времени их поверхностного натяжения. 2. Под поверхностным натяжением понимают силу, действующую на единицу длины контура поверхности и стремящуюся сократить поверхность до минимума при заданных объемах фаз | |
20. Контактно-реактивное плавление | Плавление паяемых материалов в контакте между собой или с технологическим покрытием, или с металлической прокладкой при температуре ниже температуры плавления наиболее легкоплавкого из них | |
21. Паяемость D. Lotbarkeit Е. Brazability; Solderability | Свойство материала образовывать паяное соединение при заданном режиме пайки (см. п.22) | |
РЕЖИМ И ПОКАЗАТЕЛИ ПАЙКИ | ||
22. Режим пайки D. Lotdaten Е. Brazing (soldering) data | Совокупность параметров и условий, при которых осуществляется пайка. Примечания: 1. Под параметрами понимают температуру пайки, время выдержки при этой температуре, скорость нагрева и охлаждения. 2. Под условиями понимают способ нагрева, припой, флюс (газовую среду), давление на соединяемые заготовки и т.п. | |
23. Площадь растекания припоя | ||
24. Краевой угол смачивания припоем Краевой угол D. Randwinkel Е. Contact angle | Двугранный угол между плоскостью, касательной к поверхности припоя у границы смачивания, и смоченной припоем плоской поверхностью паяемого материала. Примечания: 1. Различают равновесный краевой угол, определенный в разновеской системе «паяемый материал-припой», и неравновесный краевой угол, определенный в состоянии указанной системы, отличном от равновесного. 2. Под равновесной системой понимают систему, в которой контактирующие фазы — твердая и жидкая — находятся в условиях термодинамического равновесия | |
25. Температура смачивания D. Benetztnstemperatur Е. Wetting temperature | Минимальная температура паяемого материала и припоя, при которой происходит смачивание припоем | |
26. Температура пайки D. Е. Brazing (soldering) temperature | Температура паяемых материалов и расплавленного припоя в месте их контакта, при которой происходит формирование паяного соединения | |
27. Термический цикл пайки D. Е. Brazing (soldering) thermal cycle | Совокупность значений температуры паяемых материалов и припоя в месте их контакта, при которых происходит нагрев, выдержка и охлаждение при пайке | |
28. Температурный интервал активности паяльного флюса D. | Интервал температур, в котором паяльный флюс выполняет свои функции | |
29. Минимальная температура активности паяльного флюса | Минимальная температура в температурном интервале активного флюса | |
30. Максимальная температура активности паяльного флюса | Максимальная температура в температурном интервале активного флюса | |
31. Температура распайки D. Е. Unbrazing (unsoldering) temperature | Минимальная температура паяного соединения, при которой возможна его распайка при заданных нагрузке и скорости нагрева. Примечание: Значение нагрузки и скорости нагрева — по ГОСТ 21547-76 | |
32. Время нагрева D. Erwarmungsdauer Е. Heat time | Интервал времени нагрева паяемых материалов и припоя в месте их контакта от температуры окружающей среды до температуры пайки | |
33. Время выдержки при пайке Время выдержки Е. Soaking time | Интервал времени выдержки паяемых материалов и припоя при температуре пайки | |
34. Время охлаждения при пайке Время охлаждения D. Е. Cooling time | Интервал времени охлаждения паяемых материалов и припоя от температуры пайки до температуры окружающей среды | |
35. Общее время пайки D. Gesamte Lotzeit Е. Full brazing (soldering) time | Интервал времени, равный сумме времени нагрева, выдержки и охлаждения при пайке | |
36. Скорость смачивания D. Benetzensgeschwindigkeit Е. Wetting rate | Отношение изменения краевого угла смачивания припоем к интервалу времени, за которое произошло изменение | |
37. Скорость смачивания припоем по площади растекания припоя Скорость растекания | Отношение изменения площади растекания припоя к интервалу времени, за которое произошло изменение | |
38. Скорость нагрева при пайке Скорость нагрева D. Erwarmungsgeschwindigkeit Е. Heat rate | Отношение изменения температуры в месте контакта паяемых материалов и припоя к интервалу времени, за которое произошло изменение | |
ВИДЫ ПАЙКИ И ЛУЖЕНИЯ | ||
39. Мягкая пайка D. Weichloten Е. Soldering | Пайка при температуре, не превышающей 723 К* | |
40. Высокотемпературная пайка Твердая пайка D. F. Brazing | Пайка при температуре, превышающей 723 К* | |
41. Пайка готовым припоем | Пайка, при которой используется заранее изготовленный припой | |
42. Пайка расплавлением полуды Е. Reflow soldering | Пайка предварительно луженых заготовок или изделий без дополнительного введения припоя | |
43. Контактно-реактивная пайка | Пайка, при которой припой образуется в результате контактно-реактивного плавления | |
44. | Пайка, при которой припой образуется в результате разложения компонентов флюса | |
45. Сваркопайка | Пайка разнородных материалов, при которой более легкоплавкий материал локально нагревается до температуры, превышающей температуру его плавления и выполняет роль припоя | |
46. Капиллярная пайка D. Е. Capillary brazing (soldering) | Пайка, при которой расплавленный припой заполняет паяльный зазор и удерживается в нем преимущественно поверхностым натяжением | |
47. Некапиллярная пайка D. | Пайка, при которой расплавленный припой заполняет паяльный зазор преимущественно под действием своего веса или прилагаемой к нему извне силы | |
48. D. Е. Braze welding | Некапиллярная пайка, при которой соединяемым кромкам заготовок придается форма, подобно разделке кромок при сварке плавлением*. Примечание. Разделка кромок — по ГОСТ 2601-84 | |
_____________________ | ||
49. Флюсовая пайка (лужение) D. (Flubmittelver zinnen) Е. Flux brazing (soldering, tinning) | Пайка (лужение) с применением флюса | |
50. Бесфлюсовая пайка (лужение) D. Flubmittelloses Е. Fluxless brazing (soldering, tinning) | Пайка (лужение), при которой для удаления окислов с поверхности паяемых материалов и припоя и предотвращения их образования применяются газовые среды или создается вакуум, или разрушение окисной пленки осуществляется ультразвуковыми колебаниями или частицами твердого материала Примечание. | |
51. Пайка в активной газовой среде D. Е. Brazing in reducing atmosphere | Бесфлюсовая пайка с применением активных газов или нейтральных газов с добавкой активных газообразных веществ | |
52. Пайка в нейтральной газовой среде D. Е. Brazing in protective atmosphere | Бесфлюсовая пайка с применением инертного газа или газа, нейтрального по отношению к паяемым материалам и припою в диапазоне температур нагрева, выдержки и охлаждения | |
53. Пайка в вакууме D. Е. Vacuum brazing | Бесфлюсовая пайка с применением разреженного газа при давлении ниже 10 Па. Примечание. Разреженный газ — по ГОСТ 5197-85 | |
54. D. (Verzinnen) Е. Ultrasonic brazing (soldering, tinning) | Бесфлюсовая пайка (лужение) с применением ультразвуковых колебаний | |
55. Абразивное лужение | Бесфлюсовое лужение с применением трения паяемого материала частицами твердого материала | |
56. Абразивно-кристаллическое лужение | Абразивное лужение, при котором частицами твердого материала являются первичные кристаллы припоя | |
57. Абразивно-кавитационное лужение | Ультразвуковое лужение припоем, содержащим частицы твердого материала | |
58. Пайка паяльником D. Е. Soldering with soldering iron | Пайка, при которой нагрев паяемых материалов и припоя осуществляется паяльником | |
59. Газопламенная пайка D. Е. Flame brazing (soldering) | Пайка, при которой нагрев паяемых материалов и припоя осуществляется газовой горелкой | |
60. Пайка в печи D. Е. Furnace brazing (soldering) | Пайка, при которой нагрев паяемых материалов и припоя осуществляется в печи | |
61. Индукционная пайка D. Е. Induction brazing (soldering) | Пайка, при которой нагрев паяемых материалов и припоя осуществляется теплом, выделяющимся в них под воздействием электромагнитного поля | |
62. Пайка погружением в расплавленный припой D. Е. Dip brazing (soldering) | Пайка, при которой нагрев паяемых материалов осуществляют в ванне с расплавленным припоем | |
63. Пайка погружением в расплавленную соль D. Е. Salt-bath brazing; Flux-dip brazing | Пайка, при которой нагрев паяемых материалов и припоя осуществляется в ванне с расплавленной солью. Примечание. Расплавленная соль может быть одновременно паяльным флюсом | |
64. Пайка волной припоя D. Е. Wave soldering | Пайка, при которой нагрев паяемых материалов, перемещаемых над ванной, и подача припоя к месту соединения осуществляются стоячей волной припоя, возбуждаемой в ванне. Примечание. Под стоячей волной понимают состояние среды, при котором расположение максимумов и минимумов перемещений колеблющихся точек среды не меняется во времени | |
65. Экзотермическая пайка D. Exothermisches Е. Exothermic brazing | Пайка, при которой нагрев паяемых материалов и припоя осуществляется за счет теплоты, выделяемой при экзотермической реакции термической реакции термитных смесей | |
66. Пайка нагретым газом D. Е. Hot-gas soldering | Пайка, при которой нагрев паяемых материалов и припоя осуществляется нагретым газом | |
67. Дуговая пайка D. Е. Arc brazing | Пайка, при которой нагрев паяемых материалов и припоя осуществляется электрической дугой | |
68. Плазменная пайка | Пайка, при которой нагрев паяемых материалов и припоя осуществляется плазмой | |
69. Электроннолучевая пайка D. Е. Electron beam brazing | Пайка, при которой нагрев паяемых материалов и припоя осуществляется электронным лучом | |
70. Пайка тлеющим разрядом | Пайка, при которой нагрев паяемых материалов и припоя осуществляется тлеющим разрядом | |
71. Пайка электросопротивлением D. Е. Resistance brazing (soldering) | Пайка, при которой нагрев паяемых материалов и припоя осуществляется пропусканием через них электрического тока | |
72. Пайка световыми лучами D. F. Light rays brazing (soldering) | Пайка, при которой нагрев паяемых материалов и припоя осуществляется световыми лучами | |
73. Пайка инфракрасными лучами D. Е. Infra-red brazing (soldering) | Пайка, при которой нагрев паяемых материалов и припоя осуществляется инфракрасными лучами | |
74. Лазерная пайка D. Е. Laser brazing | Пайка, при которой нагрев паяемых материалов и припоя осуществляется лазером (излучением оптического квантового генератора) | |
75. Пайка нагретыми блоками D. Е. Block brazing (soldering) | Пайка, при которой нагрев паяемых материалов и припоя осуществляется контактирующими с ними нагретыми массивными телами | |
76. Пайка нагревательными матами D. mit Е. Heated pads brazing (soldering) | Пайка, при которой нагрев паяемых материалов и припоя осуществляется тепловыделяющими элементами, вмонтированными в термостойкие гибкие покрывала | |
77. Электролитная пайка | Пайка, при которой нагрев паяемых материалов и припоя осуществляется при их контакте с водным электролитом пропусканием постоянного электрического тока | |
78. Диффузионная пайка | Пайка, при которой образование паяного соединения совмещено с изотермической обработкой. Примечание. Изотермическая обработка обуславливает прохождение диффузии с целью направленного изменения свойств паяного соединения, в том числе кристаллизации металла шва при температуре пайки | |
79. Пайка под давлением | Пайка, при которой паяемые материалы находятся под давлением с целью уменьшения паяльного зазора | |
80. Ступенчатая пайка D. Е. Stage brazing | Пайка многошовных заготовок или изделий с поочередным образованием паяных швов, при которой не происходит распайка или образование дефектов образованных ранее соединений | |
81. Оплавление полуды | Нагрев луженой заготовки выше температуры плавления полуды с целью повышения ее качества | |
82. Одновременная пайка | Пайка многошовных заготовок или изделий с одновременным образованием паяных швов на всем их протяжении | |
83. Групповая пайка | Одновременная пайка нескольких заготовок или изделий | |
84. Механизированная пайка (лужение) D. Mechanisiertes (Verzinnen) Е. Mechanized brazing (soldering, tinning) | Пайка (лужение), осуществляемая по механизированному методу выполнения технологического процесса. Примечание. Механизированный метод выполнения технологического процесса — по ГОСТ 23004-78 | |
85. Автоматическая пайка (лужение) D. Automatisches (Verzinnen) Е. Automatic brazing (soldering, tinning) | Пайка (лужение), осуществляемая по автоматическому методу выполнения технологического процесса. Примечание. Автоматический метод выполнения технологического процесса — по ГОСТ 23004-78 | |
ПАЯНЫЕ СОЕДИНЕНИЯ И ИХ ПАРАМЕТРЫ_______________ * Эскизы соединений к терминам 88-94, 97, 101-103 приведены в ГОСТ 19249-73. | ||
86. Тип паяного соединения D. Lotverbindungsart Е. Brazed (soldered) joint type | Классификационная группировка паяных соединений, выделенная по признаку взаимного расположения и формы паяемых элементов. Примечание. Под паяемым элементом понимают часть заготовки или изделия, подвергаемую пайке | |
87. Характерное сечение паяного соединения | Сечение паяного соединения, по которому выявляют его тип | |
88. Нахлесточное паяное соединение Ндп. Паяное соединение внахлестку D. Е. Lap braxed (soldered) joint | Паяное соединение, в котором паяемые элементы соединены частично перекрывающимися взаимно параллельными поверхностями | |
89. Телескопическое паяное соединение | Нахлесточное паяное соединение труб или трубы с прутком | |
90. Стыковое паяное соединение Ндп. Паяное соединение встык D. Stumplotverbindung | Паяное соединение, в котором паяемые элементы, расположенные в одной плоскости или на одной поверхности, соединены торцовыми поверхностями | |
91. Косостыковое паяное соединение Ндп. Паяное соединение вскос D.Schrage Е. Scarf butt brazed (soldered) joint | Стыковое паяное соединение, в котором углы между торцовыми и боковыми поверхностями элементов отличны от прямого | |
92. Тавровое паяное соединение Ндп. Паяное соединение втавр D. Е. Tee brazed (soldered) joint | Паяное соединение, в котором боковая поверхность одного паяного элемента соединена с торцом другого или с его внутренней поверхностью, образованной в пересечении с первым | |
93. Соприкасающееся паяное соединение | Паяное соединение, в котором паяемые элементы соединены по линии или в точке | |
94. Комбинированное паяное соединение | Паяное соединение, представляющее различные комбинации паяных соединений нахлесточного, стыкового, косостыкового, таврового, телескопического, соприкасающегося | |
95. Согласованное паяное соединение | Паяное соединение, образованное при пайке материалов с одинаковым или близким относительным изменением их линейных размеров при охлаждении | |
96. Несогласованное паяное соединение | Паяное соединение, образованное при пайке материалов с резко отличающимся относительным изменением их линейных размеров при охлаждении | |
97. Паяный шов D. Е. Brazed (soldered) seam | Часть паяного соединения, закристаллизовавшаяся при пайке | |
98. Зона сплавления Спай D. Legierungszone Е. Alloying zone | Поверхность между паяемым материалом и паяным швом или граница между ними в сечении паяного соединения | |
99. Диффузионная зона D. Diffusionszone Е. Diffusion zone | Часть паяного соединения с измененным химическим составом паяемого материала в результате взаимной диффузии компонентов припоя и паяемого материала | |
100. Зона термического влияния D. Е. Heat affected zone | Часть паяного соединения с измененными под влиянием нагрева при пайке структурой и свойствами паяемого материала | |
101. Толщина паяного шва D. Е. Thickness of brazed (soldered) seam | Расстояние между соединенными пайкой поверхностями по перпендикуляру к ним | |
102. Длина паяного шва D. Е. Length of brazed (soldered) seam | Протяженность паяного шва вдоль перпендикуляра к плоскости характерного сечения | |
103. Ширина паяного шва D. Е. Breadth of brazed (soldered) seam | Протяженность паяного шва в характерном сечении паяного соединения | |
104. Галтельный участок паяного шва Галтель паяного шва | Часть паяного шва, образовавшаяся на наружных поверхностях паяемых элементов | |
ДЕФЕКТЫ ПАЯНЫХ СОЕДИНЕНИЙ_______________ * Дефекты: «пора», «цепочка пор», «усадочная раковина», «шлаковое включение», «трещина», «трещина продольная», «трещина поперечная», «трещина разветвленная», «микротрещина», «наплыв» — по ГОСТ 2601-84. | ||
105. Непропай | Дефект паяного соединения, проявляющийся в частичном или полном незаполнении паяльного зазора припоем | |
106. Неспай | Дефект паяного соединения, проявляющийся в отсутствии сцепления паяемого материала с материалом паяного шва | |
107. Общая химическая эрозия при пайке Общая эрозия | Дефект паяного соединения, проявляющийся в разрушении паяемого материала при пайке, развивающемся равномерно по всей поверхности его контакта с припоем | |
108. Локальная химическая эрозия при пайке Локальная эрозия | Дефект паяного соединения, проявляющийся в разрушении паяемого материала при пайке, развивающемся в отдельных участках его контакта с расплавленным припоем | |
109. Подрез при пайке Подрез | Дефект паяного соединения, проявляющийся в виде незаполненного припоем углубления в паяемом материале у галтельного участка, образовавшегося вследствие локальной химической эрозии | |
110. Паяльные остаточные напряжения | Остаточные напряжения, имеющиеся в паяном соединении после охлаждения. Примечание. Под остаточными напряжениями понимают напряжения, остающиеся в паяном соединении после устранения факторов, которые вызвали в нем пластическую деформацию: механических, термических, химических | |
(Измененная редакция, Изм. N 1). | ||
ПРИПОИ | ||
111. Многослойный припой D. Mehrschichtlot Е. Multilayer brazing alloy (solder) | Припой в виде слоев металлов или сплавов, образующих при температуре пайки сплав заданного состава | |
112. Порошковый припой D. Lotpulver Е. Powder brazing alloy (solder) | Припой в виде порошка или смесь порошков металлов или сплавов, образующая при температуре пайки припой заданного состава | |
113. Композиционный припой Ндп. Металлокерамический припой | Припой, содержащий в своем объеме наполнитель. Примечание. Под наполнителем понимают материал, применяемый для образования в паяльном зазоре системы капилляров или обеспечения специальных свойств соединения | |
114. Формованный припой D. Lotformteil Lotpulver Е. Preformed brazing alloy (solder) | Припой в виде заготовки заданной формы | |
115. Самофлюсующий припой D. enhaltendes Lot Е. Self-fluxing brazing alloy | Припой, обладающий свойствами флюса | |
116. Трубчатый припой D. Seelenlot Е. Cored solder | Припой, в форме трубки или многоканального прутка, полости в котором заполнены флюсом или компонентами припоя | |
117. Паяльная паста D. Е. Brazing (soldering) paste | Пастообразная смесь порошкового припоя с флюсом и связующим веществом или с одним из них. Примечание. Под связующим веществом понимают вещество, входящее в паяльную пасту для образования связи между частицами припоя | |
Время выдержки | 33 | |
Время выдержки при пайке | 33 | |
Время нагрева | 32 | |
Время нагрева при пайке | 32 | |
Время охлаждения | 34 | |
Время охлаждения при пайке | 34 | |
Время пайки общее | 35 | |
Галтель паяного шва | 104 | |
Десмачивание | 19 | |
Десмачивание паяемого материала | 19 | |
Длина паяного шва | 102 | |
Зазор паяльный | 15 | |
Зазор сборочный | 14 | |
Зазор сборочный под пайку | 14 | |
Затекание | 17 | |
Затекание припоя в зазор | 17 | |
Зона диффузионная | 99 | |
Зона сплавления | 98 | |
Зона термического влияния | 100 | |
Интервал активности паяльного флюса температурный | 28 | |
Лужение | 2 | |
Лужение абразивное | 55 | |
Лужение абразивно-кавитационное | 57 | |
Лужение абразивно-кристаллическое | 56 | |
Лужение автоматическое | 85 | |
Лужение бесфлюсовое | 50 | |
Лужение механизированное | 84 | |
Лужение ультразвуковое | 54 | |
Лужение флюсовое | 49 | |
Материал вспомогательный | 6 | |
Материал паяемый | 4 | |
Напайка | 1 | |
Напряжения остаточные паяльные | 110 | |
Непропай | 105 | |
Неспай | 106 | |
Облуживание | 2 | |
Оплавление полуды | 81 | |
Пайка | 1 | |
Пайка автоматическая | 85 | |
Пайка бесфлюсовая | 50 | |
Пайка в активной газовой среде | 51 | |
Пайка в вакууме | 53 | |
Пайка в нейтральной газовой среде | 52 | |
Пайка в печи | 60 | |
Пайка волной припоя | 64 | |
Пайка высокотемпературная | 40 | |
Пайка газопламенная | 59 | |
Пайка готовым припоем | 41 | |
Пайка групповая | 83 | |
Пайка диффузионная | 78 | |
Пайка дуговая | 67 | |
Пайка индукционная | 61 | |
Пайка инфракрасными лучами | 73 | |
Пайка капиллярная | 46 | |
Пайка контактно-реактивная | 43 | |
Пайка лазерная | 74 | |
Пайка механизированная | 34 | |
Пайка мягкая | 39 | |
Пайка нагревательными матами | 76 | |
Пайка нагретым газом | 66 | |
Пайка нагретыми блоками | 75 | |
Пайка некапиллярная | 47 | |
Пайка низкотемпературная | 39 | |
Пайка одновременная | 82 | |
Пайка паяльником | 58 | |
Пайка плазменная | 68 | |
Пайка погружением в расплавленную соль | 63 | |
Пайка погружением в расплавленный припой | 62 | |
Пайка под давлением | 79 | |
Пайка расплавлением полуды | 42 | |
Пайка реактивно-флюсовая | 44 | |
Пайка световыми лучами | 72 | |
Пайка ступенчатая | 80 | |
Пайка твердая | 40 | |
Пайка тлеющим разрядом | 70 | |
Пайка ультразвуковая | 54 | |
Пайка флюсовая | 49 | |
Пайка экзотермическая | 65 | |
Пайка электролитная | 77 | |
Пайка электроннолучевая | 69 | |
Пайка электросопротивлением | 71 | |
Пайкосварка | 48 | |
Паста паяльная | 117 | |
Паяемость | 21 | |
Перепайка | 13 | |
Плавление контактно-реактивное | 20 | |
Площадь растекания припоя | 23 | |
Подпайка | 12 | |
Подрез | 109 | |
Подрез при пайке | 109 | |
Полуда | 8 | |
Покрытие барьерное | 10 | |
Покрытие технологическое | 9 | |
Припайка | 1 | |
Припой | 5 | |
Припой композиционный | 113 | |
Припой металлокерамический | 113 | |
Припой многослойный | 111 | |
Припой порошковый | 112 | |
Припой самофлюсующий | 115 | |
Припой трубчатый | 116 | |
Припой формованный | 114 | |
Распаивание | 11 | |
Распай | 11 | |
Распайка | 11 | |
Растекание | 16 | |
Растекание припоя | 16 | |
Режим пайки | 22 | |
Сваркопайка | 45 | |
Сечение паяного соединения характерное | 87 | |
Скорость нагрева | 38 | |
Скорость нагрева при пайке | 38 | |
Скорость растекания | 37 | |
Скорость смачивания | 36 | |
Скорость смачивания припоем по краевому углу смачивания | 36 | |
Скорость смачивания припоем по площади растекания | 37 | |
Смачивание | 18 | |
Смачивание припоем | 18 | |
Соединение паяное | 3 | |
Соединение паяное внахлестку | 88 | |
Соединение паяное вскос | 91 | |
Соединение паяное встык | 90 | |
Соединение паяное втавр | 92 | |
Соединение паяное комбинированное | 94 | |
Соединение паяное косостыковое | 91 | |
Соединение паяное нахлесточное | 88 | |
Соединение паяное несогласованное | 96 | |
Соединение паяное согласованное | 95 | |
Соединение паяное соприкасающееся | 93 | |
Соединение паяное стыковое | 90 | |
Соединение паяное тавровое | 92 | |
Соединение паяное телескопическое | 89 | |
Спай | 98 | |
Спайка | 1 | |
Температура активности паяльного флюса максимальная | 30 | |
Температура активности паяльного флюса минимальная | 29 | |
Температура пайки | 26 | |
Температура распайки | 31 | |
Температура смачивания | 25 | |
Температура смачивания припоем | 25 | |
Тип паяного соединения | 86 | |
Толщина паяного шва | 101 | |
Угол краевой | 24 | |
Угол смачивания припоем краевой | 24 | |
Участок паяного шва галтельный | 104 | |
Флюс паяльный | 7 | |
Флюс | 7 | |
Цикл пайки термический | 27 | |
Ширина паяного шва | 103 | |
Шов паяный | 97 | |
Эрозия локальная | 108 | |
Эрозия общая | 107 | |
Эрозия при пайке химическая локальная | 108 | |
Эрозия при пайке химическая общая | 107 | |
Alloying zone | 98 | |
Arc brazing | 67 | |
Automatic brazing | 85 | |
Automatic soldering | 85 | |
Automatic tinning | 85 | |
Auxiliary material | 6 | |
Barrier coating | 10 | |
Block brazing | 75 | |
Block soldering | 75 | |
Brazability | 21 | |
Braze welding | 48 | |
Brazed joint | 3 | |
Brazed joint type | 86 | |
Brazed seam | 97 | |
Brazing | 1, 40 | |
Brazing alloy | 5 | |
Brazing data | 22 | |
Brazing in protective atmosphere | 52 | |
Brazing in reducing atmosphere | 51 | |
Brazing paste | 117 | |
Brazing temperature | 26 | |
Brazing thermal cycle | 27 | |
Breadth of brazed seam | 101 | |
Breadth of soldered seam | 101 | |
Butt brazed joint | 90 | |
Butt soldered joint | 90 | |
Capillary brazing | 46 | |
Capillary soldering | 46 | |
Cold clearance | 14 | |
Contact angle | 24 | |
Cooling time | 34 | |
Cored solder | 116 | |
Dewetting | 19 | |
Diffusion zone | 99 | |
Dip brazing | 62 | |
Dip soldering | 62 | |
Electron beam brazing | 69 | |
Exothermic brazing | 65 | |
Flame brazing | 59 | |
Flame soldering | 59 | |
Flowing | 17 | |
Flux | 7 | |
Flux blazing | 49 | |
Flux soldering | 49 | |
Flux tinning | 49 | |
Fluxless brazing | 50 | |
Fluxless soldering | 50 | |
Fluxless tinning | 50 | |
Flux-dip brazing | 63 | |
Full brazing time | 35 | |
Full soldering time | 35 | |
Furnace brazing | 60 | |
Furnace soldering | 60 | |
Heat affected zone | 100 | |
Heat rate | 38 | |
Heat time | 32 | |
Heated pads brazing | 76 | |
Heated pads soldering | 76 | |
Hot clearance | 15 | |
Hot-gas soldering | 66 | |
Induction brazing | 61 | |
Induction soldering | 61 | |
Infra-red brazing | 73 | |
Infa-red soldering | 73 | |
Lap brazed joint | 88 | |
Lap soldered joint | 88 | |
Laser brazing | 74 | |
Length of brazed seam | 102 | |
Length of soldered seam | 102 | |
Light rays brazing | 72 | |
Light rays soldering | 72 | |
Mechanized brazing | 84 | |
Mechanized soldering | 84 | |
Mechanized tinning | 84 | |
Multilayer brazing alloy | 111 | |
Multilayer solder | 111 | |
Powder brazing alloy | 112 | |
Powder solder | 112 | |
Preformed brazing alloy | 114 | |
Preformed solder | 114 | |
Rebrazing | 13 | |
Reflow soldering | 42 | |
Resistance brazing | 71 | |
Resistance soldering | 71 | |
Resoldering | 13 | |
Salt-bath brazing | 63 | |
Self-fluxing brazing alloy | 115 | |
Scarf butt brazed joint | 91 | |
Scarf butt soldered joint | 91 | |
Soaking time | 33 | |
Solder | 5 | |
Solderability | 21 | |
Soldered joint | 3 | |
Soldered joint type | 86 | |
Soldered seam | 97 | |
Soldering | 1, 39 | |
Soldering data | 22 | |
Soldering paste | 117 | |
Soldering temperature | 26 | |
Soldering thermal cycle | 27 | |
Soldering with soldering iron | 58 | |
Spreading | 16 | |
Stage brazing | 80 | |
Tee brazed joint | 92 | |
Tee soldered joint | 92 | |
Thickness of brazed seam | 103 | |
Thickness of soldered seam | 103 | |
Tinning | 2 | |
Ultrasonic brazing | 54 | |
Ultrasonic soldering | 54 | |
Ultrasonic tinning | 54 | |
Unbrazing | 11 | |
Unbrazing temperature | 31 | |
Unsoldering | 11 | |
Unsoldering temperature | 31 | |
Vacuum brazing | 53 | |
Wave soldering | 64 | |
Wetting | 18 | |
Wetting rate | 36 | |
Wetting temperature | 25 | |
Working temperature range of flux | 28 | |
Термин по | Термин по | Определение по ИСО 857-79* |
40. Высокотемпературная пайка | Твердая пайка | Операции, при которых металлические детали соединяются с помощью присадочного металла, имеющего температуру |
39. Низкотемпературная пайка | Мягкая пайка | плавления ниже, чем температура плавления соединяемых деталей и смачивающего основной металл. Основной металл не |
48. Пайкосварка | Пайкосварка | плавится при образовании соединения. |
39. Низкотемпературная пайка | Мягкая пайка | Операция при которой металлические детали соединяются с помощью присадочного металла, имеющего температуру плавления ниже температуры плавления соединяемых деталей и ниже 450 °С и смачивающего основной металл. Основной металл не плавится при образовании соединения |
40. Высокотемпературная пайка | Твердая пайка | Процесс соединения металлов, при котором во время или после нагревания расплавленный металл втягивается под действием капиллярной силы в зазор между прилегающими поверхностями соединяемых деталей. Температура плавления присадочного металла выше 450 °С, но всегда ниже температуры плавления основного металла |
48. Пайкосварка | Пайкосварка (включая пайкосварку латунью) | Метод твердой пайки, при котором соединение открытого типа получается последовательно, подобно сварке плавлением, с помощью присадочного металла, температура плавления которого выше 450 °С |
ПСр 1 Стандарт: ГОСТ 19746-2015, ГОСТ 19738-2015 Температура плавления: 225-235°C Пайка и лужение серебряных деталей. |
Проволока d от 1 мм |
ПСр 1,5 Стандарт: ГОСТ 19746-2015, ГОСТ 19738-2015 Температура плавления: 273-280°C Пайка меди и никеля со стеклоэмалью и керамикой. |
Проволока d от 1 мм |
ПСрОС 2-58 Стандарт: ГОСТ 19746-2015, ГОСТ 19738-2015 Температура плавления: 183°C Пайка и лужение меди, никеля, медных и медно-никелевых сплавов с посеребрённой керамикой, пайка посеребренных деталей. |
Проволока d от 1 мм |
ПСр 2 Стандарт: ГОСТ 19746-2015, ГОСТ 19738-2015 Температура плавления: 235-238°C Пайка меди и никеля со стеклоэмалью и керамикой. Пайка и лужение ювелирных изделий. |
Проволока d от 1 мм |
ПСр 2,5с Стандарт: ГОСТ 19746-2015, ГОСТ 19738-2015 Температура плавления: 304-306°C |
Проволока d от 1 мм |
ПСр 2,5 Стандарт: ГОСТ 19746-2015, ГОСТ 19738-2015 Температура плавления: 295-300°C Пайка и лужение цветных металлов и стали. |
Проволока d от 1 мм, Лента 2ммХ8мм |
ПСр 3Кд Стандарт: ГОСТ 19746-2015, ГОСТ 19738-2015 Температура плавления: 314-342°C Пайка меди, медных сплавов и стали по свеженанесенному медному гальваническому покрытию не менее 10 мкм. |
Проволока d от 1 мм |
ПСрОС 3-58 Стандарт: ГОСТ 19746-2015, ГОСТ 19738-2015 Температура плавления: 180-190°C Пайка и лужение меди, никеля, медных и медно-никелевых сплавов с посеребрённой керамикой, пайка посеребренных деталей. |
Проволока d от 1 мм |
ПСрОС 3-97 Стандарт: ГОСТ 19746-2015, ГОСТ 19738-2015 Температура плавления: 221-225°C Пайка и лужение меди, никеля, медных и медно-никелевых сплавов с посеребрённой керамикой, пайка посеребренных деталей. |
Проволока d от 1 мм |
ПСр 3 Стандарт: ГОСТ 19746-2015, ГОСТ 19738-2015 Температура плавления: 304-315°C Пайка меди и никеля со стеклоэмалью и керамикой. Пайка и лужение цветных металлов и стали. |
Проволока d от 1 мм |
ПСр 3,5-95 Стандарт: ГОСТ 19746-2015, ГОСТ 19738-2015 Температура плавления: 220-224°C Пайка и лужение меди, никеля, медных и медно-никелевых сплавов с посеребрённой керамикой, пайка посеребренных деталей. |
Проволока d от 1 мм |
ПСрМО 5 Стандарт: ГОСТ 19746-2015, ГОСТ 19738-2015 Температура плавления: 215-240°C Пайка и лужение меди, никеля, медных и медно-никелевых сплавов с посеребрённой керамикой, пайка посеребренных деталей. |
Проволока d от 1 мм |
ПСрОСу 8 Стандарт: ГОСТ 19746-2015, ГОСТ 19738-2015 Температура плавления: 235-250°C Пайка и лужение меди, никеля, медных и медно-никелевых сплавов с посеребрённой керамикой, пайка посеребренных деталей. |
Проволока d от 1 мм |
ПСрО 10-90 Стандарт: ГОСТ 19746-2015, ГОСТ 19738-2015 Температура плавления: 221-280°C Пайка и лужение меди, никеля, медных и медно-никелевых сплавов с посеребрённой керамикой, пайка посеребренных деталей. |
Проволока d от 1 мм |
ПСр 10 Стандарт: ГОСТ 19746-2015, ГОСТ 19738-2015 Температура плавления: 822-850°C Лужение и пайка меди, медных и медно-никелевых сплавов, никеля, ковара, нейзильбера, латуней и бронз. |
Проволока d от 1 мм |
ПСр 12М Стандарт: ГОСТ 19746-2015, ГОСТ 19738-2015 Температура плавления: 793-830°C Пайка стали с медью, никелем, медными и медно-никелевыми сплавами. |
Проволока d от 1 мм |
ПСр 15 Стандарт: ГОСТ 19746-2015, ГОСТ 19738-2015 Температура плавления: 640-810°C Пайка и лужение ювелирных изделий. Самофлюсующиеся припои для пайки меди с бронзой, меди с медью, бронзы с бронзой. |
Проволока d от 1 мм |
ПСр 25Ф Стандарт: ГОСТ 19746-2015, ГОСТ 19738-2015 Температура плавления: 645-725°C Самофлюсующиеся припои для пайки меди с бронзой, меди с медью, бронзы с бронзой. |
Проволока d от 1 мм |
ПСр 25 Стандарт: ГОСТ 19746-2015, ГОСТ 19738-2015 Температура плавления: 740 — 775 °C Пайка и лужение ювелирных изделий. |
Проволока d от 1 мм |
ПСр 37,5 Стандарт: ГОСТ 19746-2015, ГОСТ 19738-2015 Температура плавления: 725-810°C Пайка меди и медных сплавов с жарапрочными сплавами и нержавеющими сплавами. |
Проволока d от 1 мм |
ПСр 40 Стандарт: ГОСТ 19746-2015, ГОСТ 19738-2015 Температура плавления: 590-610°C Пайка меди и латуни с коваром, никелем, с нержавеющими сталями и жарапрочными сплавами, пайка свинцово-оловянистых бронз. |
Проволока d от 1 мм |
ПСр 45 Стандарт: ГОСТ 19746-2015, ГОСТ 19738-2015 Температура плавления: 665-730°C Пайка и лужение ювелирных изделий. |
Проволока d от 1 мм |
ПСрКдМ 50-34-16 Стандарт: ГОСТ 19746-2015, ГОСТ 19738-2015 Температура плавления: 685-630°C Пайка и лужение цветных металлов и стали. |
Проволока d от 1 мм |
ПСрМЦКд 45-15-16-24 Стандарт: ГОСТ 19746-2015, ГОСТ 19738-2015 Температура плавления: 615 °C Пайка и лужение цветных металлов и стали. |
Проволока d от 1 мм |
ПСр 50Кд Стандарт: ГОСТ 19746-2015, ГОСТ 19738-2015 Температура плавления: 625-640°C Лужение и пайка меди, медных и медно-никелевых сплавов, никеля, ковара, нейзильбера, латуней и бронз. |
Проволока d от 1 мм |
ПСр 50 Стандарт: ГОСТ 19746-2015, ГОСТ 19738-2015 Температура плавления: 779-860°C Пайка титана и титановых сплавов с нержавеющей сталью. |
Проволока d от 1 мм |
ПСр 62 Стандарт: ГОСТ 19746-2015, ГОСТ 19738-2015 Температура плавления: 650-723°C Пайка меди с никелированым Вальфрамом. |
Проволока d от 1 мм |
ПСр 65 Стандарт: ГОСТ 19746-2015, ГОСТ 19738-2015 Температура плавления: 695-722°C Пайка и лужение ювелирных изделий. |
Проволока d от 1 мм |
ПСр 68-27-5 Стандарт: ГОСТ 19746-2015, ГОСТ 19738-2015 Температура плавления: 655-765°C Пайка титана и титановых сплавов с нержавеющей сталью. Пайка и лужение цветных металлов и стали. |
Проволока d от 1 мм |
ПСр 70 Стандарт: ГОСТ 19746-2015, ГОСТ 19738-2015 Температура плавления: 715-770°C Пайка и лужение ювелирных изделий. Пайка титана и титановых сплавов с нержавеющей сталью. |
Проволока d от 1 мм |
ПСр 71 Стандарт: ГОСТ 19746-2015, ГОСТ 19738-2015 Температура плавления: 654-795°C Самофлюсующиеся припои для пайки меди с бронзой, меди с медью, бронзы с бронзой. |
Проволока d от 1 мм |
ПСр 72 Стандарт: ГОСТ 19746-2015, ГОСТ 19738-2015 Температура плавления: 779 °C Лужение и пайка меди, медных и медно-никелевых сплавов, никеля, ковара, нейзильбера, латуней и бронз. Пайка железоникелевого сплава с посеребрёнными деталими из стали. |
Проволока d от 1 мм |
Немного науки о меди и олове — Vintage French Copper
Между медной сковородой и ее оловянным покрытием происходит очень интересная химия.
Олово использовалось для облицовки медных кастрюль на протяжении веков по ряду причин, возможно, прежде всего потому, что олово так легко прилипает к меди. Взгляните на это видео от Mauviel, в котором показано, как они наносят олово на новенький медный горшок.
Они упрощают внешний вид: горячая сковорода, расплавленное олово, завихрение и протирание, закалка.Конечно, это совсем непросто — жестянщики Мовьеля обладают высокой квалификацией в том, что может быть очень опасным процессом, — но я хочу сказать, что олово быстро и надежно прилипает к стенкам сковороды.
Но дело в том, что эту банку снять довольно сложно. Консервы не могут просто снова нагреть сковороду и вылить из нее, как в воду, есть базовый слой, который нужно соскрести. Вы можете увидеть этот базовый слой на старинных медных кастрюлях, которые очищали старомодным способом (до изобретения средства для мытья посуды в 1940-х годах), очищая их песком.Вот три таких сковороды, прежде чем я отправил их на ретиннинг, и вы можете видеть, что базовый слой все еще там, несмотря на то, что выглядит очень жесткой очисткой.
Если вы хотите удалить этот последний слой олова, он требует сильного физического истирания. Перенесемся в 3:09 в видео о ретиннинге ниже от Sherwood Tinning (очевидно, не известного своей осторожностью со старой медью), и вы увидите, что они используют полировальный круг.
Что это за штука? Он не блестит, как олово, не плавится, как олово, и он тверже и эластичнее, чем олово.Что это такое и как оно туда попало?
Интерметаллический слой
Короткий ответ заключается в том, что базовый слой представляет собой интерметаллическое соединение, состоящее из меди и олова. Мне металлург объяснил:
Когда олово покрывается медью, образуется промежуточный слой, называемый интерметаллидом, который является своего рода «клеем» между двумя металлами и на самом деле представляет собой совершенно другой материал. Интерметаллид более твердый и хрупкий, и его нелегко удалить.
На пороге между медью (Cu) и оловом (Sn) атомы связываются, образуя сплав, который ведет себя больше как керамика, чем как металл. Интерметаллиды всегда образуются в двух вариантах (называемых фазами) с атомами в соотношении 3: 1 или 6: 5, а в случае меди и олова это создает Cu 3 Sn и Cu 6 Sn 5 . Часть футеровки из чистого олова лежит сверху и удерживается на месте интерметаллическим «клеем», как это описывает металлург. Вот почему перегретое олово не просто проливается на сковороду — интерметаллический слой удерживает олово на месте, пока его не потревожит более сильная сила (например, ваш шпатель).
Важно отметить, что это , а не бронза (CuSn), металлический сплав олова и меди. По словам металлурга,
г.Атомные связи интерметаллических материалов включают как металлические, так и ионные связи, поэтому на самом деле они не являются металлическими сплавами, такими как бронза. Это делает их твердыми и хрупкими, в отличие от бронзы, которая довольно пластична … Вы не сможете создать бронзовый сплав, не расплавив и не смешав составляющие.
Другими словами, атомы меди и олова не образуют связей, из которых состоит бронза, а вместо этого образуют разные связи, связывающие атомы в жесткую решетку.Эта жесткость делает его больше похожим на керамику — он гладкий, твердый и хрупкий. Вот почему основной слой оловянной футеровки такой упругий, и его трудно отделить от находящейся под ним меди.
Металлург также объяснил назначение флюса в процессе лужения. Я слышал, как консерваторы описывают флюс как очиститель, но я думал, что это было сделано только для того, чтобы смыть грязь или золу с поверхности. По словам металлурга, цель флюса — расчистить путь, говоря химически, для образования правильных связей между медью и оловом.
Flux — это, по сути, способ счистить поверхность, на которой вы пытаетесь создать соединение металл-металл. Обычно он состоит из кислотного элемента, который концентрируется и активируется при нагревании. Поскольку большинство металлов вступают в реакцию с атмосферой, обычно образуя оксид, необходим флюс, чтобы разъедать оксид, чтобы могла образоваться настоящая связь металла с металлом, которая создает интерметаллид.
Подумайте о мастерах по металлу за тысячелетия, которые выяснили это методом проб и ошибок!
Некоторые изображения
Если вы прорежете свою медную посуду и посмотрите на поперечное сечение олова, вы сможете увидеть интерметаллический слой.К счастью, вам не нужно этого делать — ниже представлена электронно-сканирующая микрофотография границы раздела между чистой медью и чистым оловом. Представьте, что темная медь внизу — это поверхность вашей сковороды; над ним находится слой Cu 3 Sn, слой Cu 6 Sn 5 и, наконец, на самом верху — чистое олово (Sn).
Интерметаллиды начинают формироваться в момент соприкосновения меди и расплавленного олова. Скорость нарастания слоев зависит от времени и температуры; этот конкретный образец был нагрет до 150 ° C (302 ° F) в течение 1000 часов, и, как вы можете видеть на диаграмме выше, слой объединенного Cu 3 Sn и Cu 6 Sn 5 составляет 18.74 микрометра (мкм) или 0,018 миллиметра толщиной.
Но вот в чем дело: реакция продолжается даже при комнатной температуре. Атомы олова довольно хорошо диффундируют в медь и при небольшой тепловой энергии легко связываются с образованием молекул Cu 6 Sn 5 . (Фактически, значительная часть недавней промышленной химии предотвращает образование интерметаллида медь-олово, поскольку он мешает работе паяных печатных плат.) Учитывая большее количество тепла (или времени, или того и другого), Cu 6 Sn 5 преобразуется в Cu 3 Sn.(Фаза Cu 3 Sn более химически устойчива, поэтому именно сюда попадают атомы.) Это происходит довольно медленно при комнатной температуре, но ускоряется, когда вы готовите на сковороде на большом огне.
Это показано на схеме ниже. Думайте о каждой стопке как о поперечном сечении вашей жестяной облицовки с течением времени: слева ваша свежая луженая сковорода со слоем чистого олова поверх узкого слоя интерметаллида. Со временем ваша сковорода выглядит как средний столбец: больше чистого олова превратилось в Cu 6 Sn 5 , а затем в Cu 3 Sn.В конце концов, жестяная банка вашей сковороды будет выглядеть как стопка справа, где почти не остается свободного олова, а весь интерметаллид превращается в Cu 3 Sn. Превращение происходит медленно при комнатной температуре и быстрее при повышении температуры — например, при готовке.
Это означает, что за многие годы использования жестяная подкладка на вашей сковороде образует твердый и упругий базовый слой. Базовый слой прикрепляет олово к меди и помогает удерживать чистое рыхлое олово на месте.Этот процесс был инициирован процессом горячего лужения, но он продолжается прямо сейчас, даже когда ваша сковорода стоит на вашей полке. В конце концов — через десятилетия — все олово будет преобразовано в Cu 3 Sn.
Скорее всего, вы протинируете свою кастрюлю до того, как будет израсходована вся банка. Но что было бы, если бы вы этого не сделали? Как назло, могу вам показать.
Пример
Обратите внимание на эту сковороду диаметром 31 см со странной подкладкой. Эта сковорода много использовалась и стала довольно горячей, как это часто бывает со сковородками.Подкладка похожа на тусклую оловянную посуду с крошечными комочками и пятнами олова по всей поверхности.
На фото ниже крупным планом видно, что поверхность не похожа на обычную жестяную подкладку. Есть участки матово-серого цвета с пятнами кускового металла сверху. (Там также есть немного коричневой приправы — это сковорода, которую я часто использую, и на ней собраны некоторые полимеризованные масла.) Я показал эту фотографию металлургу, который сказал, что пятнистые серые пятна являются обнаженными интерметаллическими соединениями, а комки наверху это чистое олово, которое осталось.
Мне интересно то, что это одна из моих самых любимых сковородок. Готовится красиво — в частности, кажется, неплохо выдерживает сильный жар. Я часто использую все свои консервированные сковороды, и в то время как другие собрали несколько комков и пятен то тут, то там, поверхность этой не изменилась. По словам металлурга, это имеет смысл: «Со временем интерметаллид будет расти, потребляя любое свободное олово, поэтому размазывание будет происходить реже, поскольку свободное олово станет тоньше, в конечном итоге оставив только интерметаллический слой.”
Кроме того, они довольно низко прилипают, по моему опыту, больше, чем мои сковороды Mauviel с их блестящей новой жестью. Он не обладает характеристиками покрытия из PFTE, такого как тефлон, с характеристиками , отличными от , но интерметаллические области кажутся похожими под моими пальцами, гладкими и твердыми, как яичная скорлупа. Интерметаллиды в целом имеют более низкий коэффициент трения, чем чистые металлы, и они часто используются в промышленности в качестве покрытий для металлических подшипников. Это наводит на мысль, что интерметаллид медь-олово на поверхности этой сковороды может работать как варочная поверхность с низким прилипанием, так же (если не лучше), как чистое олово, которое оно заменило.(Посмотрите еще раз на фото выше — кажется, что полимеризованные масла не прилипают к интерметаллическим участкам!)
Заключение
Свойства интерметаллида медь-олово подсказывают мне некоторые возможные объяснения трех явлений, которые я наблюдал на своих луженых медных сковородках.
Перегретое олово имеет тенденцию оставаться на месте, поскольку его стабилизирует интерметаллический слой. Олово плавится при 450 ° F (232 ° C), но интерметаллид медь-олово имеет гораздо более высокую температуру плавления: Cu 6 Sn 5 плавится при 779 ° F (415 ° C), а Cu 3 Sn при намного выше 1248 ° F (676 ° C).Это означает, что интерметаллический слой остается твердым и стабилизирует футеровку при температурах, значительно превышающих точку плавления олова. Это также объясняет, почему для того, чтобы размазать жестяную подкладку, требуются некоторые физические действия, такие как соскабливание или перемешивание — расплавленное олово остается на месте, пока не будет приложена внешняя сила.
Старый слой олова устойчив к смазыванию лучше, чем новый. По мере того, как интерметаллический слой растет и слой чистого олова становится тоньше, все больше этих чистых атомов олова находится рядом с интерметаллическим слоем и стабилизируется им.
Старый слой олова сопротивляется соскабливанию до меди. Одна из уязвимостей оловянной футеровки по сравнению с более твердыми материалами, такими как нержавеющая сталь, заключается в том, что резкие царапины или царапины могут протолкнуть мягкий слой олова до меди под ним, что ускоряет потребность в новой футеровке. Олово имеет твердость по Виккерсу менее HV 80, но по данным Ассоциации медной промышленности, интерметаллиды медь-олово имеют твердость около HV 300, почти такую же твердость, как и медь. (Вот почему можно случайно стереть олово с помощью губки для чистки, но лужайки должны соскребать медно-оловянный интерметаллид с помощью шлифовального круга.Это означает, что прочный керамический интерметаллический слой с большей вероятностью выдержит абразивное давление, отклонение кухонной утвари или губки для чистки до того, как достигнет меди.
Это предлагает мне заманчивую возможность: жестяные накладки улучшаются с возрастом и использованием. Может быть, лучшее, что вы можете сделать для своих консервных сковород, — это готовить на них много! — чтобы вагонка созрела и стала лучше готовиться. Что вы думаете?
Если вы ученый — а особенно металлург! — Я хотел бы получить известие от вас, даже если — , особенно , если! — Вы не согласны или можете опровергнуть мои идеи.Пожалуйста, оставьте комментарий или напишите мне по адресу vfc at vintagefrenchcopper dot com . Спасибо!
Источники
Помимо информации, полученной от моего друга-металлурга, я использовал несколько источников для получения информации.
Интерметаллические поперечные сечения: Ян, Пинг-Фэн и Лай, И-Шао и Цзянь, Шэн-Жуй и Чен, Цзюнн и Чен, Жун-Шэн. (2008). Наноиндентирование механических свойств интерметаллидов Cu6Sn5, Cu3Sn и Ni3Sn4, полученных диффузионными парами.Материаловедение и инженерия: А. 485. 305–310. 10.1016 / j.msea.2007.07.093.
Диаграмма роста интерметаллического слоя:
https://www.copper.org/applications/industrial/DesignGuide/performance/coppertin03.html
(Обратите внимание, что на диаграмме Cu6Sn5 неправильно обозначен как Cu3Sn5 в белой области каждого креста. раздел.)
Преобразование твердости по Бринеллю в твердость по Виккерсу:
http://www.carbidedepot.com/formulas-hardness.htm
Отличное обсуждение твердости как концепции и различий между измерениями твердости по Роквеллу, Бринеллю и Виккерсу:
https: // www.machinemfg.com/metal-hardness/
Значения твердости для Cu и Sn:
https://en.wikipedia.org/wiki/Hardness_of_the_elements_(data_page)
Твердость по Виккерсу для интерметаллида медь-олово:
https://www.copper.org/applications/industrial/DesignGuide/performance/friction03.html
Также спасибо читателю Филу за поправку со шлифовального круга на полировальный! Я признателен за это!
Как это:
Нравится Загрузка …
Лужение старых медных горшков / сковородок своими руками протертым вручную — пошаговые инструкции: 10 шагов (с изображениями)
Новый и улучшенный второй этап лужения был опубликован г-ном. .Buscrendore из Лейпсика в журнале Journal fur Fabrik, производство, и Handlung в октябре 1799 года. Да, верно, 1799 !
Он действительно теряет некоторые знания, поэтому ниже его полный текст, второй этап лужения выделен жирным шрифтом.
«Хорошо известно, что медные и латунные сосуды нельзя безопасно использовать для приготовления пищи или для хранения пищевых продуктов, особенно содержащих кислоты.
Также хорошо известно, что лужение, применяемое в обычных условиях манера не долговечна, быстро изнашивается при чистке и по этой причине должна часто обновляться.Некоторые поэтому предложили эмаль для кухонных принадлежностей из меди; что, действительно, было бы чрезвычайно хорошо и было бы намного безопаснее для здоровья, чем нечистое олово, смешанное со свинцом, часто используемое для лужения; но, к сожалению, эмаль слишком дорога и легко ломается при малейшем ударе по сосуду; чего нельзя избежать всегда.
Следующий процесс лужения не представляет опасности со стороны ядовитых ингредиентов, так как в нем не используется свинец; лужение также чрезвычайно прочно, увеличивает прочность медного сосуда и защищает его от воздействия кислот гораздо дольше, чем обычное лужение.
Когда сосуд подготовлен и очищен обычным способом, ему необходимо придать шероховатость изнутри, ударив по грубой наковальне, чтобы лужение лучше держалось и было более тесно связано с медью. Затем процесс лужения следует начинать с совершенно чистого олова с добавлением соляного аммиака вместо обычного колофония.
Поверх этого лужения, которое должно покрывать медь равномерно и равномерно, необходимо нанести второе более твердое покрытие, поскольку первое образует лишь своего рода среду для соединения второго с медью.Для этого второго лужения вы используете чистое зернистое олово, смешанное с цинком в соотношении два к трем, которое также необходимо наносить с нашатырным спиртом гладким и ровным, чтобы нижний слой мог быть полностью им покрыт.
Это покрытие, которое из-за добавления цинка становится довольно твердым и твердым, затем следует забить гладильным молотком после того, как оно было должным образом протерто и промыто мелом и водой, чтобы оно стало более твердым. и приобретает гладкую компактную поверхность.
Емкости и утварь можно лужить с обеих сторон. В этом случае, после того, как они подвергнутся достаточному нагреву, их необходимо окунуть в жидкую банку, что означает одновременное лужение обеих сторон.
Поскольку это лужение чрезвычайно прочно и имеет красивый цвет, который он всегда сохраняет, его можно использовать для различных видов металлических инструментов и сосудов, которые, возможно, потребуется защитить от ржавчины ».
Советы и рекомендации для с использованием медных кастрюль
1.)
Не прогревайте медные горшкиПоскольку медь так хорошо проводит тепло, она очень быстро нагревается. Жестяная подкладка может расплавиться всего за 30 секунд, в зависимости от размера сковороды.
2.)
Избегайте истирания жестиЖестяная подкладка определенно изменит цвет со временем. В зависимости от того, что вы готовите, он станет темно-серым или почти черным. У вас может возникнуть соблазн чистить его до блеска после каждого использования, но это значительно сократит срок службы жестяной подкладки.Держите его в чистоте — но отпустите. Если вы готовите пищу, попробуйте наполнить медную сковороду водой и небольшим количеством средства для посуды, затем варить на медленном огне в течение 15 минут. Вы удивитесь, насколько легко приготовленная пища очищается. Меньше смазки на локтях и меньше износа жести!
3.)
Не поджаривайте в медных кастрюляхПомните, что жестяная подкладка плавится всего при температуре около 450 градусов F. Чтобы поджарить мясо при сильном нагревании, выберите чугун, алюминий или нержавеющую сталь вместо меди посуда.
4.)
Используйте деревянную / силиконовую посуду с медными горшками.Не царапайте жестяную поверхность для приготовления пищи металлической посудой.
5.) Полировка 101
Тут определенно две точки зрения. Некоторым нравится яркий вид полированной меди — некоторым нравится мягкий потускневший вид «медного пенни». Делай свое дело; В любом случае медь сделает СВОЮ вещь. Если вы находитесь в полировальном лагере — вот отличный пищевой полироль:
Растворите 1 т соли в 1/2 стакана белого уксуса и добавьте муки, чтобы получилась жидкая паста (например, клей Элмера).Храните в небольшой посуде Tupperware под раковиной.
После мытья сковороды окуните влажное бумажное полотенце в лак, протрите медью примерно 30 секунд, затем смойте теплой водой с мылом.
СУХОЙ КАНАЛ для предотвращения водяных пятен.
Если вы будете делать это после каждого использования, потребуется около 30 секунд дополнительного времени. Ждать полгода и потом полировка потребует гораздо больше усилий!
Лужение старых медных кастрюль / сковородок, вытертое вручную — пошаговая процедура
Разумно купить себе медную сковороду, а почему бы и нет? Это один из лучших проводников с точки зрения металла и намного превосходит другие металлы по многим другим параметрам!
Короче говоря, после включения плиты достаточно нескольких минут, чтобы тепло равномерно распространилось по сковороде.Требуемое количество тепла меньше, а распределение более сбалансировано. И, наконец, у вас есть возможность лучше контролировать температуру!
Почему подкладка из олова?Напоминаем, что медь — очень реактивный материал. Таким образом, покрытие из олова предотвращает реакцию кислой пищи, такой как томатная паста. Взаимодействие меди с некоторыми продуктами питания может сделать вкус пищи довольно странным и даже привести к пищевому отравлению при длительном хранении.
Большинство новых медных кастрюль имеют стальную футеровку, что делает их более долговечными.
Но и с этим есть проблемы — липкость и меньшая проводимость. Однако со сталью эти шансы меньше, чем с оловом. Старые горшки, которые можно найти в магазинах, уже облицованы оловом и имеют старинный вид, что делает их красивее.
Вещи, о которых следует помнить при выполнении процессаЕсли вы достали старую посуду, убедитесь, что вы начали с нескольких мерок. Для начала можно полностью доверять толщине сковороды.
Еще одна вещь, на которую стоит обратить внимание, — это тяжесть сковороды. Сочетание увеличенной толщины и большего веса делает его более прочным. Слишком большая толщина также может быть проблемой, делая ее слишком тяжелой для использования.
Толщина посуды составляет от 1 мм до 3 мм. Чем он тяжелее, тем лучше. Для начала, если вы хотите быстро определить качество, убедитесь, что он тяжелый. Более старые обычно имеют соединения типа «ласточкин хвост», которые обычно образуются путем сколачивания медных листов вместе.
Многие современные модели обычно не имеют стыков. И если вы не уверены в цене, то да, вы можете заплатить больше за более тяжелую модель, поскольку она является лучшей.
Ступеньки для лужения медных горшковЗдесь все шаги, с которыми вам придется ознакомиться. Давай начнем;
1. Очистка кастрюли / сковородыЕсли у вас старая сковорода, этот шаг является обязательным. Очистить такие сковороды может быть немного сложно, но со временем вы все исправите.Обязательно замачивайте сковороду в горячем уксусе или воде, в зависимости от того, что вам удобно.
Выдержите 30 минут во влажном состоянии, чтобы удалить грязь и придать сковородке блеск. Вы можете тереть его, если он полностью очищен. Щелкните ссылку и прочтите полное руководство по очистке Coper
. 2. Сковорода для пикловТравление — еще один важный этап процесса лужения. Теперь вам нужно замочить сковороду в ведре со смесью сильной кислоты и воды.
На этом этапе, поскольку вы используете кислоту, безопасность является обязательной, поэтому убедитесь, что все, что вы делаете, вы делаете в перчатках и надлежащей защите.
Кислота удаляет весь оставшийся нагар, жир, а также съедает остатки олова со сковороды. Через несколько часов быстро и осторожно вымойте сковороду и нанесите последний слой скраба Brillo. Теперь вы можете, наконец, покрыть его свежей жестью и завершить процесс лужения.
3. лужение сковородыДля начала посыпьте внутреннюю часть сковороды немного измельченным нашатырным спиртом.Итак, как это работает? Он просто работает за счет образования дыма, вызванного реакцией с аммиаком. Лучше носить маски, так как дым может вызвать проблемы с дыханием.
Нашатырный спирт подвергается реакции, в результате которой образуется дым, который, в свою очередь, приводит к образованию ржавчины. Этот дым вреден, поэтому разумно надеть маску. Нашатырный спирт действует как флюс, поэтому олово прилипает к горшку. После того, как дым начнет увеличиваться, добавьте к нему гранулы олова.
Теперь олово расплавится, когда горшок станет горячим.Теперь продолжайте перемешивать жидкую банку и добавьте еще немного нашатырного спирта, а затем протрите жидкую банку с помощью тампона сантехника и перчаток.
Необходимо убедиться, что сковорода должным образом нагревается, чтобы олово и медь могли склеиться должным образом. В этом процессе вы можете увидеть, как олово плавится и достигает блестящей формы с переходным цветом, как только оно нагревается.
4.Повторить процессВ первый раз все никогда не бывает безупречным, как и в этом случае.Скорее всего, во время первого испытания ваша сковорода покрыта излишками олова, но это совершенно нормально.
Кроме того, есть вероятность, что вы используете избыточное количество олова, что сделает его грубым. Но да, повторением нескольких раз, проб и ошибок вы наверняка сможете добиться успеха в этом процессе лужения.
Для более легкого и равномерного нагрева вы также можете попробовать переставить горшок, но убедитесь, что вы никогда не перегреваете его, иначе вы можете сжечь ткань, которую вы используете для протирания, и предотвратить склеивание.Для аккуратного и точного обогрева всегда можно использовать фонарик сантехника.
Могут быть моменты, когда вам нужно начинать с самого начала, а могут быть случаи, когда стороны не обработаны хорошо. В таких случаях их нужно переделывать заново.
Это было бы удобно для более точного нагрева, и всегда есть следующий раз. Но да, это может быть не всегда ваша вина, а иногда это может зависеть только от самой кастрюли / кастрюли.
ЗаключениеЛужение может быть интересным процессом, но это, конечно, не снижает его важности.Это хороший метод, если вы хотите, чтобы ваши сковороды / кастрюли не вступали в реакцию с кислотными материалами, а также если вам нужны сковороды / кастрюли длительного пользования или вы хотите сэкономить деньги, используя старые.
Хотя это может быть сложно и довольно опасно, поэтому лучше надеть перчатки и маски. Пока вы соблюдаете осторожность, все в порядке.
Retinning Медные кастрюли и сковороды в Великобритании и США
Почему Newlyn Tinning Retinning Service?
Retinning каждой медной сковороды, медного котла или другого предмета медной посуды, нуждающегося в замене футеровки, будет тщательно очищен, полностью залужен и отполирован небольшими партиями, чтобы обеспечить наилучшую отделку вашей посуды с использованием старинного метода ручной протирки лужение и только самая чистая олово пищевого качества.
Единственный выбор для ретинирования качественной медной посуды!
• Retinning
• Глубокая очистка для удаления всего нагара и смазки
• Изменение формы и удаление вмятин
• Затяжка заклепок
• Механическое удаление старой облицовки
• Повторное лужение чистым оловом
• Полироль для наружных поверхностей
Единственная в Великобритании услуга по повторному лужению, которая в настоящее время не облагается НДС, с мгновенным калькулятором стоимости.
Все емкости должны быть отправлены в Newlyn Tinning в подходящей, прочной, хорошо упакованной коробке с большим количеством места.Ручки торчат или заклинивают не идеально!
За дополнительную упаковку будет взиматься дополнительная плата в размере 3,50 фунтов стерлингов, если товары прибывают в непригодной для возврата коробке.
Пожалуйста, приложите записку с вашим именем, адресом, адресом электронной почты и номером телефона.
Вы также можете использовать эту распечатываемую форму заказа в формате pdf.
Newlyn Tinning может вдохнуть новую жизнь в вашу медную посуду с полным повторным лужением и восстановлением.
Лужение, протираемое вручную. Единственный способ получения качественной посуды.Традиционный и лучший.
Единственная в Великобритании служба по повторному лужению, которая в настоящее время не облагается НДС.
Найдите время, чтобы посетить раздел «Что такое хорошая сковорода?» гид здесь.
Все емкости должны быть отправлены в Newlyn Tinning в подходящей, прочной, хорошо упакованной коробке с большим количеством места. Ручки торчат или заклинивают не идеально!
За дополнительную упаковку взимается дополнительная плата в размере 3,50 фунтов стерлингов, если товары прибывают в непригодной для возврата коробке.
Пожалуйста, приложите записку с вашим именем, адресом, адресом электронной почты и номером телефона.
Вы также можете использовать эту распечатываемую форму заказа в формате pdf.
По окончании работ вам будет выслан счет со всеми необходимыми платежными реквизитами.
При оплате чеком или почтовым переводом, пожалуйста, включите его в свою доставку, отправленную на номер Steven Pearse .
Стоимость обратной доставки указана в разделе «Платежи и доставка».
Сковорода овальная или квадратная?
Если чаша овальная или квадратная, для расчета диаметра следует использовать среднее значение длины и ширины.(L + W) ÷ 2 = Диаметр
Для круглых плоских крышек используйте диаметр в мм, умноженный на 0,10 (1,00 фунта стерлингов за см).
Если используется овальная или квадратная форма, следует использовать среднее значение двух длин.
За большие предметы, стоимость которых превышает 90 фунтов стерлингов, может взиматься дополнительная плата в размере 20%.
Newlyn Tinning в настоящее время не занимается лужением чайников. Пожалуйста, ищите гальванику.
В процессе замены футеровки будет использоваться только самая чистая олово пищевого качества, так что ваши любимые кастрюли и сковороды будут готовы к многолетней безупречной эксплуатации.
Олово не придает запаху и не придает вредным побочным продуктам, PFOA, которые, как известно, образуются с антипригарными поверхностями PTFE. Олово на 100% безопасно для пищевых продуктов и уже более 9000 лет используется для изготовления медной посуды!
Каждая полученная мною кастрюля или сковорода проходит тщательный 5-этапный процесс.
1. Прежде всего, каждая сковорода подвергнется глубокой очистке, чтобы удалить все масла, смазки и нагар, чтобы получить чистый предмет для дальнейшей обработки.
2. Затем каждая сковорода будет изменена, а все заклепки проверены и затянуты.
3. После формования сковороды будут очищены от всех оксидов, оставляя молекулярную звуковую поверхность чистой и яркой.
Мелкие трещины и трещины от пайки теперь можно при необходимости отремонтировать с помощью серебряного припоя пищевого качества. Извините, необходимо будет обсудить основные трещины, пробелы и неисправности.
4. Теперь сковорода готова для лужения и будет иметь традиционную белизну для защиты внешней поверхности и специально разработанный флюс Newlyn Tinning, нанесенный на поверхность для приготовления пищи. Затем вся сковорода нагревается до нужной температуры и повторно консервируется.Консервирование всей посуды сразу даст лучшее покрытие по сравнению с лужением по частям, как это делают многие.
Используемый процесс лужения представляет собой традиционный метод протирания вручную. Единственный выход на качественную медную посуду !!!!
5. Наконец, каждая сковорода будет очищена снаружи и отполирована, чтобы выявить красивый блеск меди.
Если вы видите бледно-розовый, голый медный или зеленый зеленый цвет, самое время для повторного лужения!
Средний срок обработки заказа составляет от 2 до 4 недель с момента получения до возврата, в зависимости от потребности в услугах.
Для получения помощи с ценами на повторное лужение и восстановление
, пожалуйста, используйте страницу контактов
Вы ремонтируете медную посуду без покрытия?
Да, Newlyn Tinning может это восстановить!
Предлагается полная глубокая очистка и восстановление ваших ценных кондитерских изделий, консервов и другой посуды для кондитерских изделий, не требующей подкладки.
Отполировано до зеркального блеска с использованием Osborne Canning Compound. Полировальная паста на растительной основе, популярная в пищевой промышленности.
Свяжитесь с нами для получения подробной информации.
Зачем нужна луженая медная проволока?
Зачем нужна луженая медная проволока?
Написано в июне 2019 г. | Тони Холдерби, Региональный менеджер по продажам в Service Wire Company
Единственное назначение электрического провода и кабеля — проводить электрический ток от одной точки к другой, но если кабель начинает корродировать, он может быстро выйти из строя и привести к потере рабочих характеристик.Хотя чистая медь довольно устойчива к коррозии, луженые медные проводники предотвращают ускоренную коррозию во влажной и загрязненной среде .
Защита от коррозии меди
Луженая медь в основном используется для защиты от окисления и коррозии. В климате, где медь подвергается длительному воздействию воды, кислород соединяется с металлом и образует оксид меди, ослабляя связи металла. Еще хуже, если провод попадет в соленую воду.По мере того, как образуется больше этого оксида, он ослабляет целостность меди, делая ее хрупкой и рассыпчатой - процесс, известный как коррозия. Едкий медный провод менее эффективен при перемещении электричества и может представлять угрозу безопасности.
Покрывая чистую медь тонким слоем олова, он может усилить естественные свойства меди, придав ей дополнительную защиту от воды, погодных условий и воздействия других коррозионных элементов при сохранении той же проводимости. Луженую медную проволоку также легче припаять к соединениям, поскольку олово является ключевым элементом при пайке, обеспечивая защиту всех частей провода от коррозии.
Применение луженой меди
Луженая медная проволока особенно полезна на очистных сооружениях, подземных подземных системах и проектах, подверженных избыточному воздействию нефти, газа или воды. Луженая медь без покрытия часто используется в коммунальных проектах на Северо-Востоке и в окружающей среде, подверженной избыточному воздействию солей хлорида натрия (морская вода) .
При выборе неизолированной или луженой меди окружающая среда должна быть определяющим фактором при выборе провода.Луженая медь может продлить срок службы вашего кабеля, но ее не так легко модернизировать во всех проектах. Прогнозирование и планирование потенциально агрессивных сред может предотвратить полную замену рабочих мест в будущем.
ИТОГ:
Луженые медные проводники в основном используются на очистных сооружениях, в системах метро и других загрязненных средах, подверженных длительному воздействию избытка воды. Оловянное покрытие меди защищает провод от коррозии и преждевременного выхода из строя.
Преимущества луженой меди:
- Защищает от коррозии
- продлевает срок службы кабеля
- Легко припаять
- Такая же проводимость, как у чистой меди
ПРОВОДНИКИ ЛОЖЕННЫЕ
КомпанияService Wire предлагает одножильные или многопроволочные луженые проводники в различных изделиях, в том числе:
Сопутствующие товары:
луженая медь VS голая медь
Преимущества луженой меди невозможно отрицать.Следуйте вместе, пока мы показываем, насколько это важно.
Что такое луженая медь?
Что ж, краткий ответ заключается в том, что луженая медь — это медь, покрытая основным сплавом, например припоем. известное как олово. Звучит просто, но это еще не все. Сама медь обладает многими полезными характеристиками, что делает ее очень желанной, однако у нее есть недостатки. Здесь в игру вступает лужение. Лужение производится по нескольким причинам. Прежде всего, он усиливает природные свойства меди, делает его лучше приспособленным к влажности, высоким температурам и влажным средам, поэтому он отличается высоким качеством морской провод.
Когда дело доходит до проводов и кабелей, можно использовать ножницы самых разных размеров и стилей. ошеломляющий. Один из самых важных аспектов выбора правильной проволоки для вашего проекта — долговечность. Это особенно актуально при работе с морской провод. Как долго прослужит провод? Как часто и насколько сложно будет производить замену? Именно такие вопросы привели к развитию лужения. медь. Каковы преимущества луженой меди по сравнению с чистой медью?
Преимущества луженой меди
Использование луженой меди — простой и эффективный способ предотвратить потускнение или потускнение медного проводника. окисляется.Вы, наверное, видели медь, когда она окисляется, она становится зеленой. Статуя Свободы — известный пример окисления меди. Что заставляет это происходить? Это химическая реакция поверхности металла с кислородом, присутствующим в воздухе, которая вызывает коррозию или окисление части металла и образование соответствующего оксида металла на поверхности.
Знаете ли вы, что луженый медный провод 12-го калибра может служить до десяти раз дольше, чем аналогичный неизолированный медный провод 12-го калибра? Поскольку олово устойчиво к коррозии и не окисляется, покрытие помогает защитить находящуюся под ним медь.Это предотвращает дополнительный износ, который может сократить срок службы неизолированного медного кабеля на годы. Это особенно важно, если рабочая температура провода превышает 100 градусов Цельсия. При более высоких температурах коррозионная стойкость меди снижается, что делает оловянное покрытие ценным для защищая провод в этом состоянии. Луженая медь также очень желательна для любой морской электроники. Поэтому его выбирают при изготовлении морской провод.
Почему медь луженая?
Медь обладает высокой проводимостью и довольно устойчива к коррозии.Эти факты в сочетании с его долговечностью делают его идеальным для электрических применений. Проблема возникает, когда медь используется во влажной среде или в помещении с высокой влажностью. В этих условиях медь гораздо быстрее подвергнется коррозии и ослабнет. Есть ли способ предотвратить это? Да. Путем лужения меди. Могу ли я залудить собственный медный провод? И да и нет. Концы провода можно зачистить с помощью инструмента для зачистки проводов и легко залудить. Для этого процесса требуется всего несколько инструментов и шагов. Однако он не действует так сильно, как вся проволока, покрытая оловом.Медная проволока лужится с помощью процесса, известного как гальваника.
Каталожные номера
The Tin Plating Process: A Step-By-Step Guide
https://www.distributorwire.com/blog/tinned-copper-vs-bare-copper/
http://www.belden.com/blog/broadcastav/in-defense-of-tinned-copper.cfm
http://www.